Crystal Growth
Crystal growth – materials development
Investigating novel quantum phases requires not only state of the art equipment but also samples of highest quality. These samples are often synthesized by ourselves right here at the institute and subsequently investigated at low temperatures, high magnetic fields, or high pressure.
Every solid state physicist, at least every experimentalist, needs samples to work with. These could come in form of powders, pellets, single crystals, lumps, ribbons, etc. Often sizes of a few millimeters along a side corresponding to masses of a few milligrams are sufficient. But why do we grow samples by ourselves? Why don’t we simply buy them or ask someone more familiar with crystal growth, like a chemist or a material scientist, to grow them for us? There are at least three good reasons.
- The samples are grown in order to answer a specific question directly related to physics. For example, how does the magnetic ordering develop when element A in the compound ABC is fully or partially replaced by element X? Do we approach a quantum critical point where unconventional superconductivity or other exotic ground states can emerge? Do we understand the physics well enough to model and describe the behavior? The vast majority of such interesting compounds are not commercially available. Either because the demand is too low or, more often, because the material is novel and the synthesis by means of an industrial standard process not established. This holds true in particular for alloy series. Chemists, on the other hand, are often more interested in finding and describing new crystal structures. Growing and optimizing a particular compound with a well-known crystal structure is usually not in the focus of a chemist’s research activity. However, detailed knowledge of the crystal structure is of fundamental importance for understanding the physical properties of a material.
- The quality of a sample is characterized by a physical measurement. Understanding novel effects like quantum phase transitions often requires exceptionally good samples. However, standard methods like chemical analysis or X-ray diffraction alone often don’t provide the necessary information. Only low temperature measurements of, for example, specific heat or magnetization can tell whether the sample quality is sufficient. Performing and analyzing these measurements requires a profound knowledge of the relevant physics. But only those measurements allow to further optimize the crystal growth process. Performing both the low temperature experiment and the crystal growth in one group, or even by one and the same person, allows us to find the optimal parameters for the synthesis in a most efficient way.
- Science is no place without competition. Even if one or more groups are able to synthesize an interesting material in good quality, the samples are not always accessible. Staying at the cutting-edge of solid state physics requires quick access to novel materials of all kinds.
Equipment and Techniques
In the following, the crystal growth equipment and the different growth techniques are briefly described.
Box furnaces
These furnaces work pretty much like the oven in a kitchen. However, we operate at temperatures between 500°C and 1200°C which significantly exceeds the values typically used for cooking meals. These furnaces are used for solid state reactions or flux growth. For the former one, the composition of the starting material is identical to the composition of the desired compound. For the latter one, the composition differs and/or other elements are added, primarily in order to lower the melting temperature.
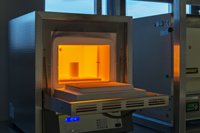
Vertical tube furnaces
Operate at temperatures of up to 1450°C. The sample chamber (tube) can be kept under constant argon flow in order to avoid an oxidation of compound and crucible. A well-defined temperature gradient can be obtained by adjusting the sample position (i.e. by moving the sample towards the cold end). This is particularly useful for the single crystal growth of congruently melting materials (Bridgeman technique).
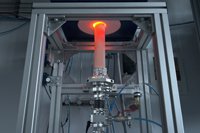
Arc melting furnace
A large electrical current between electrode and sample ionizes an inert gas creating a high-temperature plasma. This allows to melt and mix elements and compounds with high melting points of more than 3000°C or to seal tantalum and niobium crucibles.
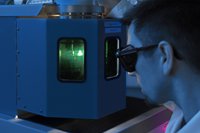
Mirror furnace
A powerful light source and focusing mirrors create temperatures of more than 2000°C at the sample position. Mainly used for single crystal growth of high-melting compounds (congruently melting with low vapor pressure).
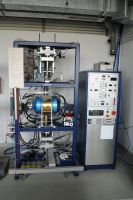
Glass bench
A hydrogen-oxygen torch is used to seal quartz ampoules. The samples can be sealed under vacuum or argon in order to avoid oxidation. A vacuum line allows pumping on four ampoules simultaneously. Quartz ampoules are used at temperatures of up 1200°C. The torch is set up in a fume hood in order to prevent inhalation of crystalline silica dust.
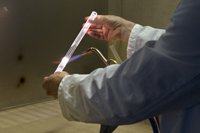
Glow boxes
to be completed...