Sustainable processing of foundry materials
Activities focus on researching and establishing sustainable energy and material cycles in the foundry industry. The first step is to reduce the consumption of resources wherever possible and then to organise the remaining resources in such a way that as much as possible can be reused. The reuse of waste heat and used materials requires a holistic view of the individual processes in the foundry as part of process chain optimisation and coordination. For example, in order to make efficient use of waste heat from the melting and casting process, consumers are needed that can make sensible use of thermal energy at lower temperature levels.
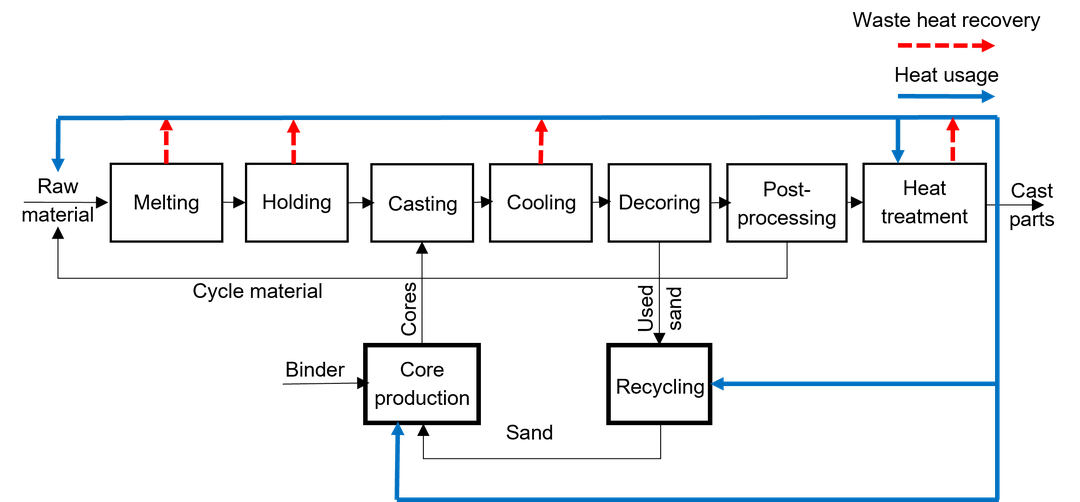
In order to improve foundry processes in the long term with this research strategy, the strategic goals are systematically broken down into sub-aspects and developed sequentially from fundamental research to application-oriented research. The following processes are currently under active research:
- We are working on processes for inorganic core production and core recycling that can be operated at low temperatures using waste heat. This not only makes environmentally friendly inorganic core technology more technically attractive but also saves large amounts of energy, particularly in the thermal regeneration of used sand.
- In the field of high-pressure die-casting, we are also working on reducing scrap and optimising component properties through the use of multi-material systems to make components lighter and more efficient.