Mechanical testing
Quasi-static testing
In the field of quasi-static testing, the working group has various machines at its disposal in a load range from a few mN to 250 kN. Furthermore, it is possible to measure superimposed load conditions (e.g. additional transverse loads and/or torsion up to 2000Nm). On the one hand, micromechanical investigations as well as classical and modified methods for the determination of characteristic values are carried out with these. One focus of the research activities here is the development and implementation of new test methods, e.g. for fibre-reinforced thermoplastics or hybrid fibre composites.
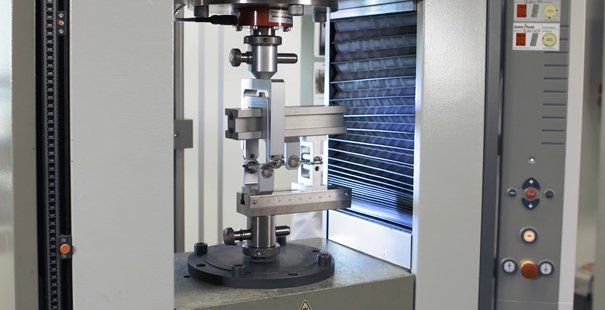
Dynamical testing
Servohydraulic universal testing machines up to a load range of 250kN are available for carrying out the measurements. The main focus of the research work is the investigation of "spectrum loading" of fiber composites as well as the combination with secondary test methods such as acoustic emission analysis, image correlation and thermography for early damage detection. In addition, tests are carried out to determine the notched bar impact strength and - in collaboration with Fraunhofer IGCV - investigations are carried out on "Compression after Impact" (CAI).
Creep testing
A creep testing machine with a load range of 50kN is available for the determination of material properties under static load. The main focus of the research work is the material class of fibre-reinforced thermoplastics. In addition to the determination of creep strength, investigations are carried out to determine the validity of the "time-temperature superposition" (TTS) principle.
Temperatur range
Especially for the testing of fibre reinforced composites, numerous testing devices are available for measurements in a temperature range from -70°C to 250°C. Special fixtures also allow the temperature range to be extended to -196°C in cryo baths and to over 2000°C in an inert gas atmosphere. For all temperatures, measuring systems are available for direct determination of the test specimen strain and for optical recording of the fracture process.
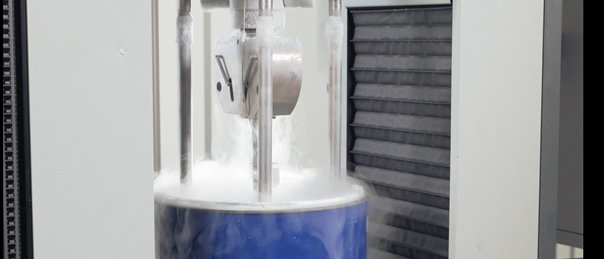
Optical strain measurement
Three optical extensometers and three measurement systems for digital image correlation are available for carrying out the measurements. These allow a reliable determination of the longitudinal and transverse strain when the test specimens are loaded. For the image correlation systems, the full-surface determination of the strain tensor also allows a detailed analysis of material degradation as well as comparison with numerical calculation methods.
Acoustic emission analysis
We are happy to combine mechanical tests with other (secondary) measuring methods such as acoustic emission analysis.
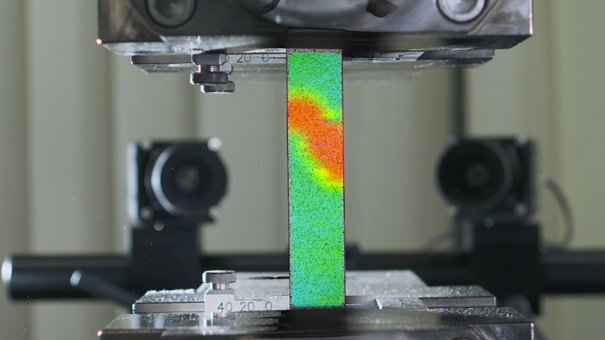