Projects
Current projects
In the following you will find a short overview of our current research projects.
AI-based acoustic quality assurance of foundry cores
AI-based acoustic quality assurance of foundry cores
Funded by: AI Production Network Augsburg
Duration: 01/25 -12/25
Data-driven Materials Processing (Prof. P. Lechner)
Content:
For foundry cores, there is no quality assurance method suitable for series production that can find hidden cracks that occur during storage. Therefore, a test setup is being developed that enables the cores to be tested by the non-destructive impulse excitation method. The resulting acoustic data is analyzed in the frequency range using machine learning methods in order to detect defects.
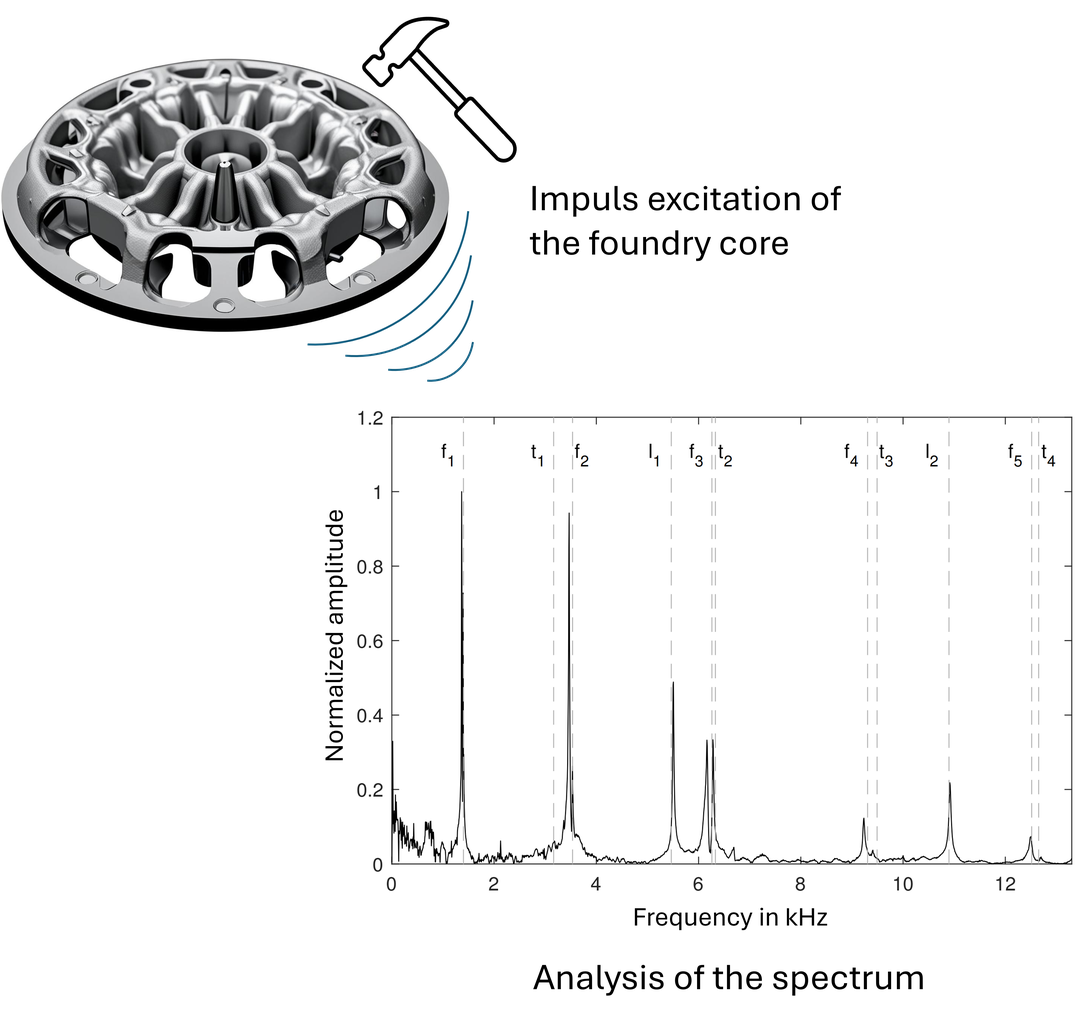
- Phone: + 49 821 598 - 69413
Email: philipp.lechner@uni-auni-a.de ()
A real-time capable surrogate model for the Friction Stir Welding process
A real-time capable surrogate model for the Friction Stir Welding process
Funded by: AI Production Network Augsburg
Duration: 01/25 -12/25
Data-driven Materials Processing (Prof. P. Lechner)
Content:
A coupled thermo-mechanical simulation of friction stir welding is being developed. This simulation is used to calculate training data with which coupled physics-informed machine learning models are trained. These real-time capable models will be validated using experimental data and will be able to calculate the process quality in real time. The aim is for this model to be integrated into the process as a feedforward control in order to adjust the process force and speeds.
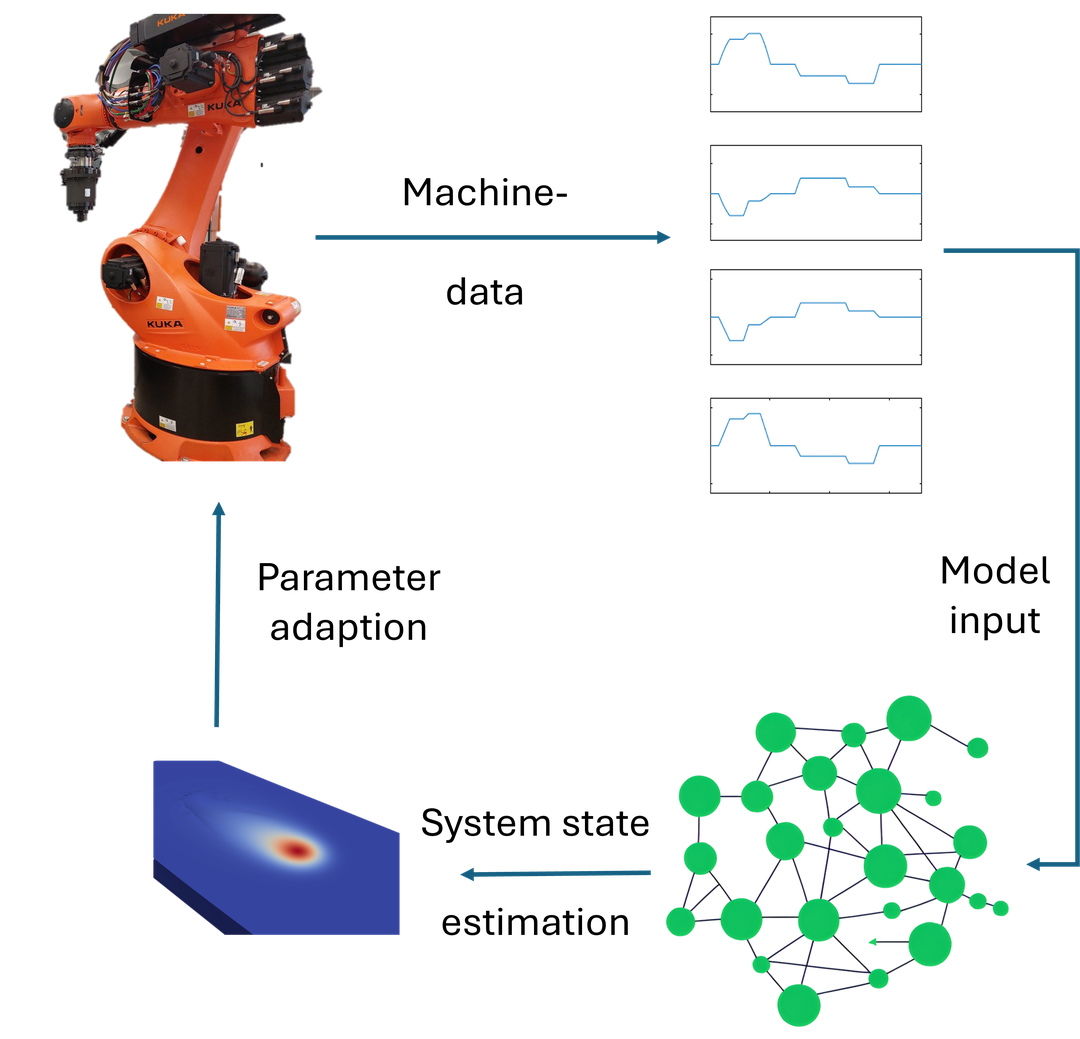
- Phone: + 49 821 598 - 69413
Email: philipp.lechner@uni-auni-a.de ()
Data-based quality inspection of foundry cores using modal analysis
Data-based quality inspection of foundry cores using modal analysis
Funded by: German Research Foundation (DFG)
Duration: 12/24 – 12/26
Data-driven Materials Processing (Prof. P. Lechner)
Content:
Quality assurance is a central aspect of modern mass production in general and core production in particular. Quality assurance for core production and subsequent metal casting is comparatively complex compared to other mass production processes such as metal forming and machining. On an industrial scale, cores are currently inspected only visually before being used in the casting mold. Fine and closed cracks are often overlooked. Material defects such as increased moisture absorption can also not be detected in this way. These defects lead to scrap after casting, which can only be classified as such after a considerable consummation of resources.
The aim of the present project is to investigate the methodological basis for non-destructive quality assurance of foundry cores. Core defects, which are caused either by the manufacturing process or subsequent storage, are often not detectable from the outside, which is why it is necessary to inspect the entire volume. Resonance testing in combination with modal analysis will be used for this purpose. Within the scope of the research project, methods will be developed not only to distinguish between good parts and scrap, but also to localize defects. For this purpose, the geometric as well as the material properties including their statistical distribution are characterized. This enables a spatially resolved quantification of the measurement uncertainty and finally a localization of defects in foundry cores. Ultimately, this leads to a decision whether a foundry core can be used reliably in the subsequent casting process or should be classified as scrap.
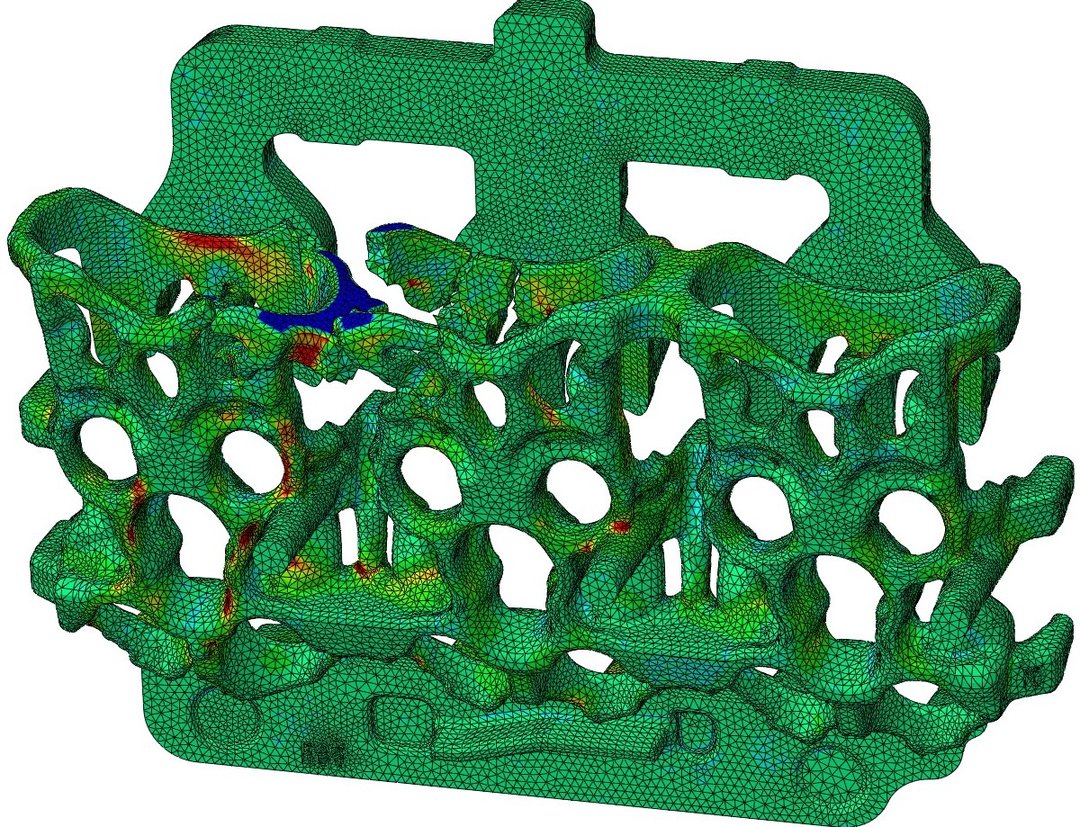
- Phone: + 49 821 598 - 69413
Email: philipp.lechner@uni-auni-a.de ()
FORinFPRO
FORinFPRO - Intelligent Manufacturing Processes & Closed-Loop Production
Funded by: Bavarian Research Foundation
Duration: March 01, 2024 – February 31, 2027
Mechanical Engineering (Prof. M. Sause)
Hybrid Materials (Prof. K. Weidenmann)
Content:
How can self-adaptive control systems for machines, plants, and process chains be implemented to learn from past process steps and adapt to future process requirements? This question is at the core of the new Bavarian research consortium FORinFPRO. The solution aims not only to contribute to higher product quality but also to enhance robustness with increased resource efficiency through the use of recycled materials in various processes. This will be investigated in the specific case of manufacturing lightweight components. To produce complex components from composite materials, innovative manufacturing processes will be enabled to meet the challenges posed by a self-adaptive process in terms of sensing, process, modeling, and control. The research methodology aims not only to advance the control of individual processes but also to realize a complex process chain that enables global control at the overall process level.

- Phone: +49 821 598-69142
Email: matthias.merzkirch@uni-auni-a.de ()
- Phone: 0821 / 598 - 69168
Email: joel.schukraft@mrm.uni-augsburgmrm.uni-augsburg.de ()
TurnKI
TurnKI - Artificial Intelligence for Monitoring Multi-Spindle Turning Processes
Funded by: Bavarian Consortium Research Program (BayVFP) of the Free State of Bavaria, Funding Line "Digitalization"
Duration: January 01, 2024 – December 31, 2025
Mechanical Engineering (Prof. M. Sause)
Content:
Within the TurnKI project, inspired by the AI Production Network Augsburg, a sensor-based process monitoring system for multi-spindle turning machines is to be researched. The research objective is to explore a real-time monitoring system capable of detecting, classifying, and quantifying workpiece and tool deviations in a complex multi-spindle turning process. To achieve this, a measurement system will be employed that monitors the machining process through vibration-based analyses, such as structure born noise analysis and vibration analysis using acceleration sensors. The real-time detection of process deviations and interpretation of sensor-detected variations will be achieved through artificial intelligence methods, particularly machine learning. Based on the monitoring solution, the identification of deviations aims to reduce scrap and selectively sort out defective products.

- Phone: +49 821 598-69142
Email: matthias.merzkirch@uni-auni-a.de ()
AI4FSW
AI4FSW – Artificial Intelligence for Friction Stir Welding
Funded by: Bavarian Consortium Research Program (BayVFP) of the Free State of Bavaria, Funding Line "Digitalization"
Duration: October 01, 2023 – September 31, 2026
Mechanical Engineering (Prof. M. Sause)
Content:
Within the project, motivated by the AI Production Network Augsburg, a multisensory process monitoring system for robot-based and portal-based friction stir welding is to be researched. The system aims to contribute to quality management and reduce subsequent inspection efforts. To achieve this, a sensor system will be designed to enable reliable monitoring. In addition to selecting various measurement techniques, there is a focus on the targeted determination of signal characteristics that allow a precise description of the process. These must be determined in real-time for online monitoring. The signal features obtained in this way are then intended to be incorporated into an artificial neural network, which will be trained with the corresponding process states/defects. Finally, the reliability and transfer potential of the system and AI will be assessed using a demonstrator component.
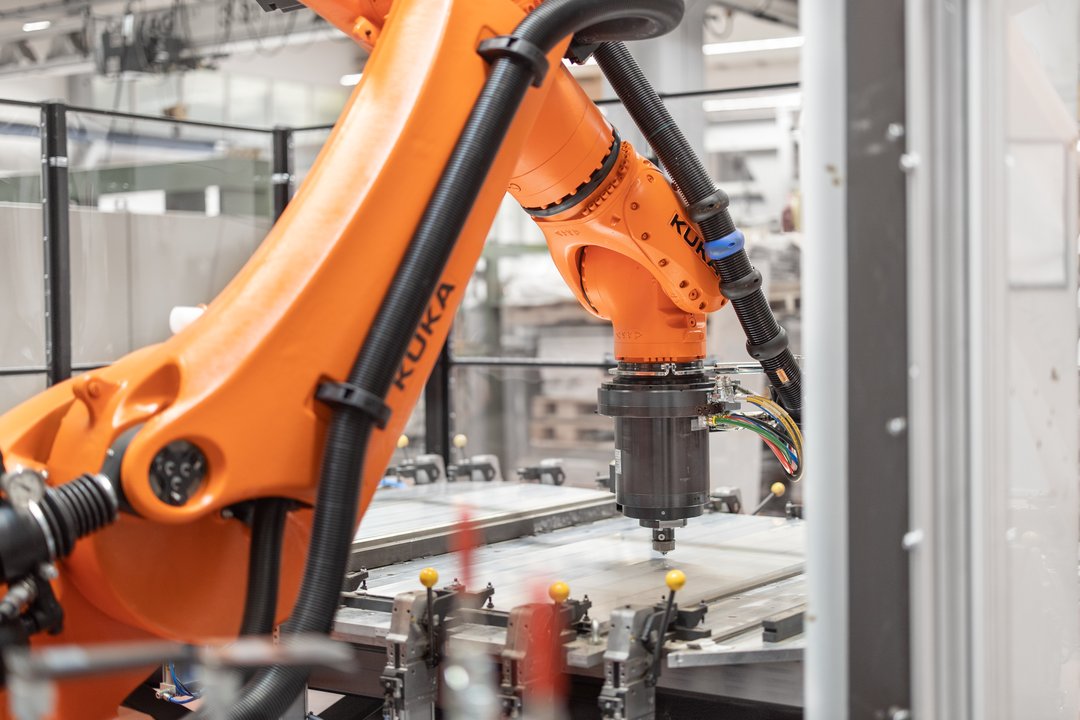
- Phone: +49 821 598-69142
Email: matthias.merzkirch@uni-auni-a.de ()
KoKIRo
KoKIRo - Kognitives, KI-gesteuertes Roboter-Montagesystem (Cognitive, AI-controlled Robot Assembly System)
Funded by: Bavarian Consortium Research Program (BayVFP) of the Free State of Bavaria, Funding Line "Digitalization"
Duration: July 01, 2023 – June 30, 2026
Mechanical Engineering (Prof. M. Sause)
Content:
The KoKIRo project focuses on developing an Industry 4.0-capable, cognitive, and flexibly configurable robot and assembly system. The project aims to address various challenges in manufacturing, such as high energy costs, supply chain issues, and a shortage of skilled workers. The objectives include developing a digital twin of the cognitive, AI-driven robot and assembly system, implementing a manufacturer-independent, universally applicable, real-time AI-control concept and ensuring a RAMI4.0-compliant system architecture using Industry 4.0 components. The key components include a collaborative robot (cobot), which is a robot designed for direct interaction with humans within a shared workspace; AI-guided real-time control is a system driven by artificial intelligence for real-time operations and multi-axis, real-time sensor technology where the sensors are tailored to specific assembly tasks to enhance precision and adaptability. The prototyping and validation within this project include three use cases to autonomously recognize tasks, reconfigure itself, and delicately manage the assembly process. Examples include automated peg-in-a-hole, screw handling and pressing or riveting processes.
Project partners: Fraunhofer IGCV, pro-micron GmbH, robominds GmbH and azero GmbH.
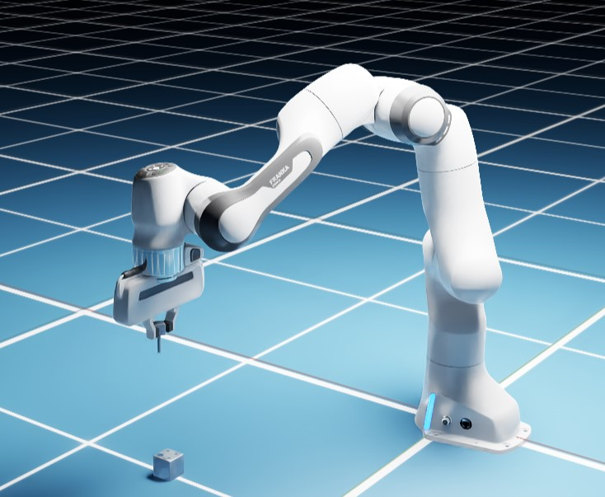
- Phone: +49 821 598 - 69420
Email: navya.prakash@uni-auni-a.de ()
Multi-scale simulation of molding materials for inorganic binders using binder-jet-3d-printing
Multi-scale simulation of molding materials for inorganic binders using binder-jet-3d-printing
Funded by: German Research Foundation (DFG)
Duration: 06/23 -06/25
Data-driven Materials Processing (Prof. P. Lechner)
Content:
In recent years, 3D printing has been developed as a technology for the production of sand cores for casting processes, particularly for rapid prototyping and low-volume foundry applications. However, due to the layered structure, this process differs significantly from classical core shooting, especially in terms of the density levels achieved.
The aim of the proposed project is to better understand the 3D printing process of sand cores in order to identify the influence of process variables on the final product. This will ensure the high quality of the printed sand cores for specific applications, while minimising the high cost of measurement and the reliance on expert knowledge and empirical values.
To this end, the proposed project will create a digital model - closely accompanied by relevant experimental studies - that represents the layer-by-layer structure of the sand core layers during 3D printing. Based on micro-computed tomography images of industrially used sands, the bulk of the sand grains will be simulated under the influence of the binder on already printed layers. Subsequently, a simulative and experimental evaluation of the mechanical, thermal and flow properties of the printed sand cores is planned.
A deeper understanding of the microscopic processes involved in the 3D printing of sand cores will serve as a basis for the further development of materials from an environmental perspective and as a basis for optimising the printing process itself.
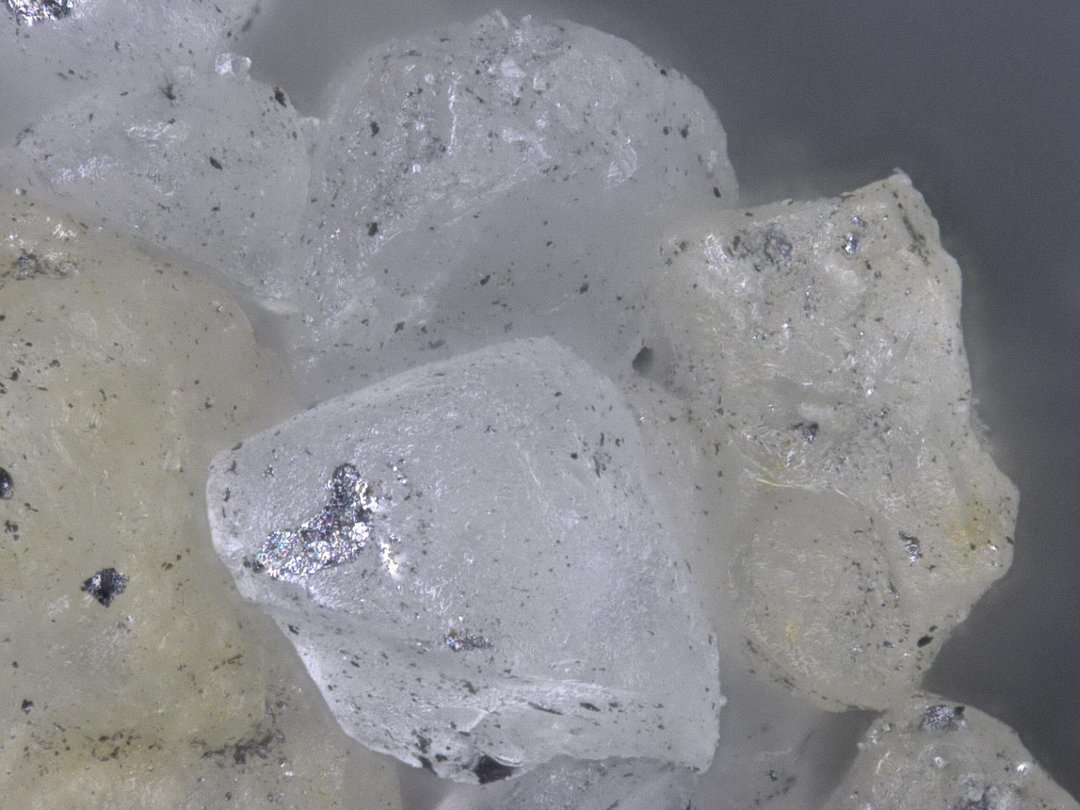
- Phone: + 49 821 598 - 69413
Email: philipp.lechner@uni-auni-a.de ()
KAXFLUX-H2
KAXFLUX-H2
Funded by: Bavarian State Ministry for Economic Affairs, Regional Development and Energy
Program: research grant
Duration: 01.01.2022 – 31.12.2025
Mechanical Engineering (Prof. M. Sause)
Content:
The research project "KAXFLUX-H2" has the goal of a complete virtual representation of the cooling process in an axial flux drive for aerospace application with the help of cryogenic hydrogen. The project is carried out in cooperation with the Augsburg Technical University of Applied Sciences. The aim is to develop an axial flow motor with cryogenic hydrogen cooling that can significantly increase the efficiency of a hydrogen-electric drive train in aircrafts through intelligent system architecture. At the University of Augsburg, the topics of material selection/development with topology optimization for use at cryogenic temperatures, associated process technology and material processing are being researched. Incorporating multiphysics simulation, the focus is on thermo-mechanical modeling and simulation of the stator respecting the entire system at cryogenic temperatures.
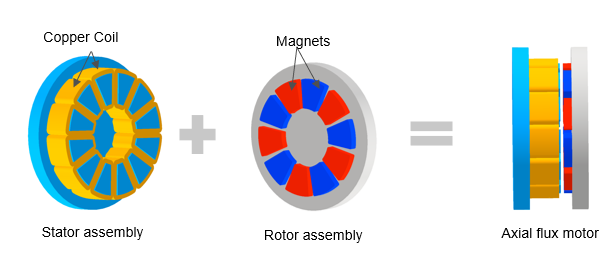
- Phone: + 49 821 598 - 69162
Email: anna.trauth@mrm.uni-augsburgmrm.uni-augsburg.de ()
Completed research projects
In the past, various projects were carried out together with research and application partners. The gallery presents an overview of the projects.
MakeKryo III - Mechanical-physical material behavior at cryogenic temperatures
Funded by: Federal Ministry of Economic Affairs and Climate Action (BMWK)
Duration: 01.11.2022 - 31.10.2024
Mechanical Engineering (Prof. M. Sause)
Content:
A comprehensive and reliable determination of characteristic values of fiber-reinforced composites at cryogenic temperatures has so far been very restricted. In the first two project phases, test concepts and methods were developed for the determination of compression and shear as well as fracture mechanical properties as well as adhesive bonding for fiber composites at very low temperatures. Continuing on this basis, the project now aims to develop new testing solutions for the integration of secondary measurement methods, such as digital image correlation, acoustic and electromagnetic emission, at low temperatures.

- Phone: + 49 821 598 - 69162
Email: anna.trauth@mrm.uni-augsburgmrm.uni-augsburg.de ()
ODIN – Optimized Design for Inspection
Funded by: European Union
Program: COST Action 18203
Duration: 02.10.2019 - 01.08.2024
Mechanical Engineering (Prof. M. Sause)
Content:
Within the EU-COST network we provide the representation of the Federal Republic of Germany and the lead of WP5 - Data management and signal processing. The goal of this expert network is to develop the technical standards for the use of structural monitoring systems (SHM) for aviation applications within the next four years. Within WG5, the work focuses on analysis strategies, data reduction methods and reliability of the measurement systems used.
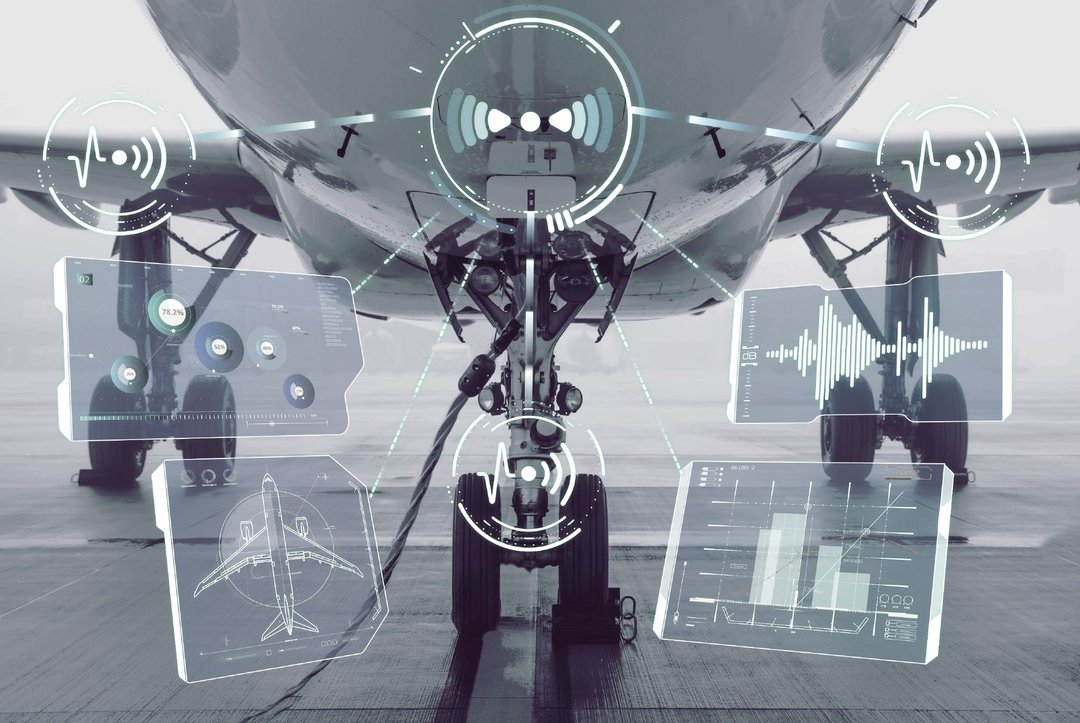
- Phone: +49 821 598 - 69161
Email: markus.sause@mrm.uni-augsburgmrm.uni-augsburg.de ()
MakeKryo II - Materialkennwertermittlung
Funded by: DLR Space Administration
Duration: 2021-2022
Mechanical Engineering (Prof. M. Sause)
Content:
Comprehensive and reliable determination of characteristic properties of fiber-reinforced composites at cryogenic temperatures has been possible only to a very limited extent so far. In a first project phase, test concepts and methods to determine compressive and shear properties of various fiber-reinforced composites at very low temperatures were already developed and validated. Based on this knowledge, this second project phase aimed to continue with the development of new test solutions to identify fracture mechanical parameters and to characterize bonded joints at very low temperatures.
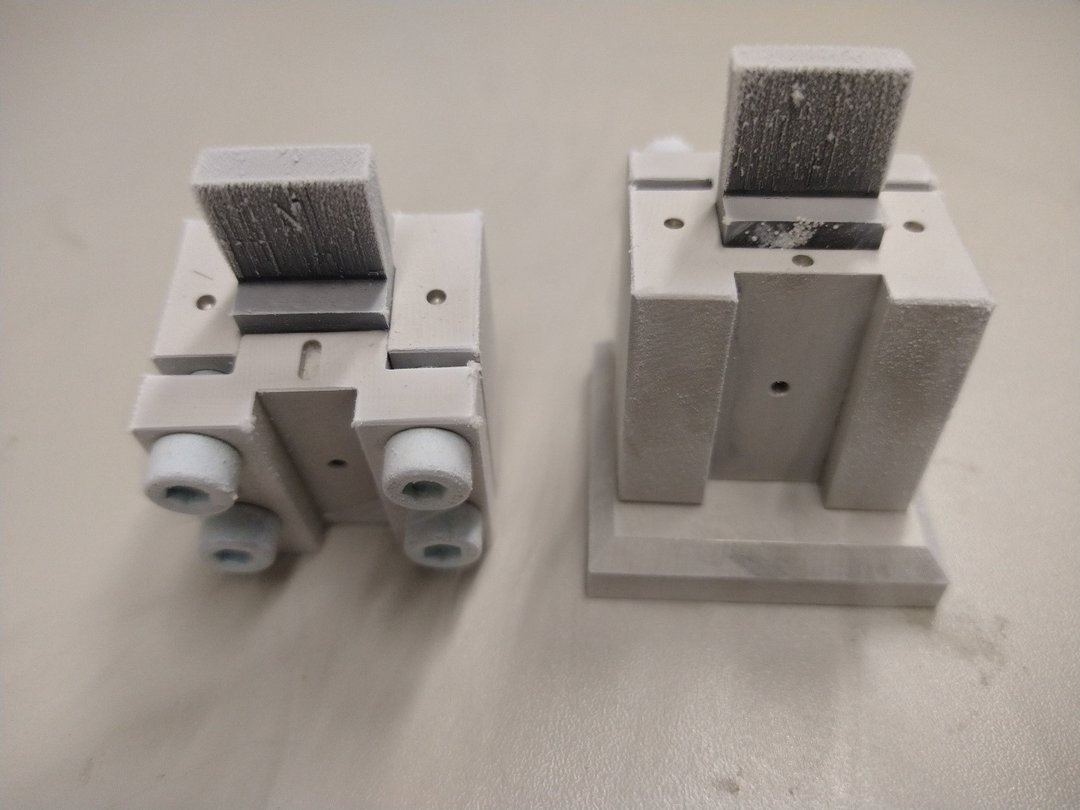
- Phone: +49 821 598 - 69161
Email: markus.sause@mrm.uni-augsburgmrm.uni-augsburg.de ()
Correlation between material microstructure and electromagnetic emission
Funded by: DFG Sachbeihilfe
Duration: 2020-2022
Mechanical Engineering (Prof. M. Sause)
Content:
This DFG project was concerned with the investigation of the fundamental relationships between the microstructure of materials and the generation of electromagnetic emission (EME) during the fracture process. EME is caused by the imbalance of charge carriers, due to the breaking of bonds and which is additionally set in motion by the dynamics of the fracture process. The influence of different parameters on the electromagnetic signals was investigated in more detail by series of measurements across material classes and then mapped in simulations. The understanding of the source mechanism was further extended and also the sensor technology was further developed in an application-oriented manner.
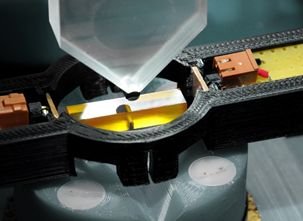
- Phone: +49 821 598 - 69161
Email: markus.sause@mrm.uni-augsburgmrm.uni-augsburg.de ()
Manufacturing and characterization of interpenetrating metal-ceramic composites based on highly homogeneous foam structures
Content:
The project investigated a highly homogeneous ceramic foam and an interpenetrating metal-ceramic composite made from it by gas pressure infiltration.
The microstructure can be transferred by CT reconstruction into a model suitable for numerical simulation of the mechanical and thermal properties of both the ceramic foam and the interpenetrating composite. Methodological developments and the transfer of evaluation methods to metal-ceramic interpenetration composites exhibited novelty character in both the experimental and numerical areas of material characterization and led to a deeper understanding of the mechanisms of action in the material system.
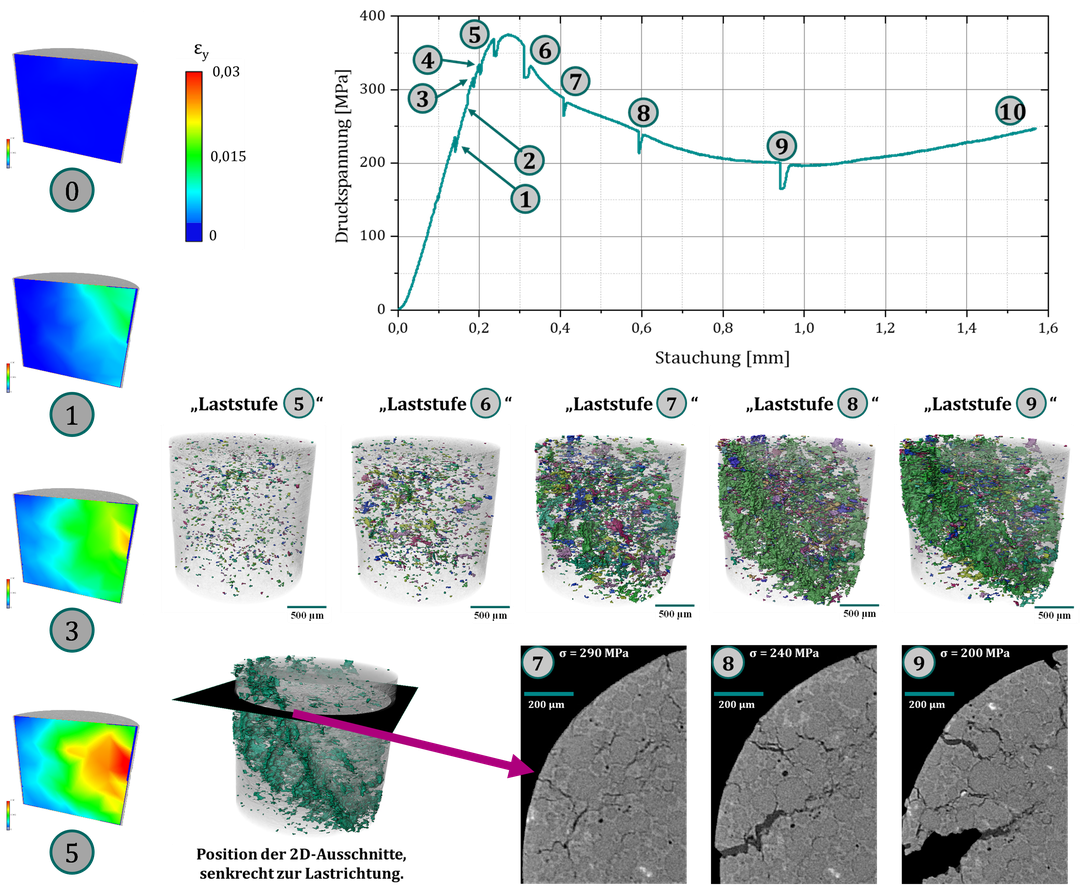
- Phone: + 49 821 598 - 69160
Email: kay.weidenmann@mrm.uni-augsburgmrm.uni-augsburg.de ()
SmartCut – Smart solutions for machining processes
Funded by: bayme vbm – KME Programm
Duration: 2021-2023
Mechanical Engineering (Prof. M. Sause)
Content:
Machining is a process step that is in many cases of central importance for product quality. Within the project machine and sensor data were used to increase tool life, reduce scrap and enable continuous quality monitoring of machining processes. For this purpose, modern machine learning methods were applied to real process data to demonstrate the concrete potential and to make the methods evaluable and available for companies.
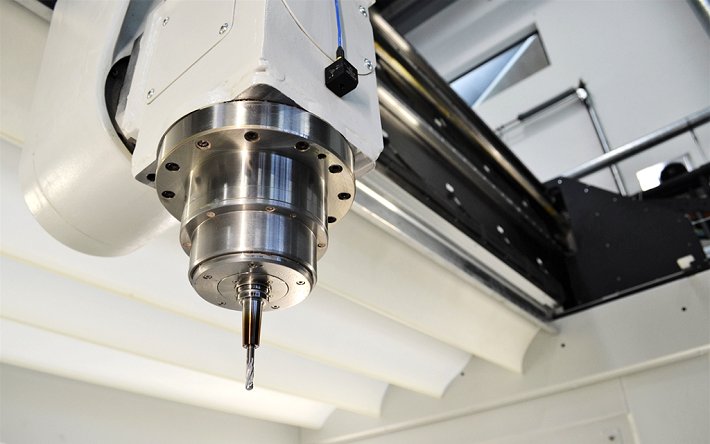
- Phone: +49 821 598 - 69161
Email: markus.sause@mrm.uni-augsburgmrm.uni-augsburg.de ()
Liquid metal infiltrated interpenetrating composites based on metallic glass - processing, characterization and modeling
Funded by: German Research Foundation (DFG)
Program: Individual Reasearch Grants
Duration: 01.07.2019 - 30.06.2023
Hybrid Composite Materials (Prof. K. Weidenmann)
Content:
In this project an interpenetrating metal matrix composite reinforced with a metallic glass (Ni60Nb20Ta20) and a eutectic AlSi12-matrix was manufactured and characterized. Laser powder bed fusion was used to manufacture an open-porous lattice-like preform from amorphous powder. Subsequently, the preform was infiltrated with the AlSi12-matrix in a gas pressure infiltration process. In the process, the amorphous structure of the metallic glass was largely maintained. Due to the manufacturing process, the preform has an anisotropic structure which is reflected in the results of the structural, mechanical, and thermal characterization carried out. The results of the in-situ and ex-situ mechanical characterization show that the composite has a significantly higher compressive strength in the manufacturing direction than transversely to the manufacturing direction, and a different failure behavior was observed in both directions. TEM studies in correlation with the in-situ investigations show that good interfacial bonding has been achieved. Finally, the experimental results were validated with analytical models of thermal expansion and elastic properties and an FE model.
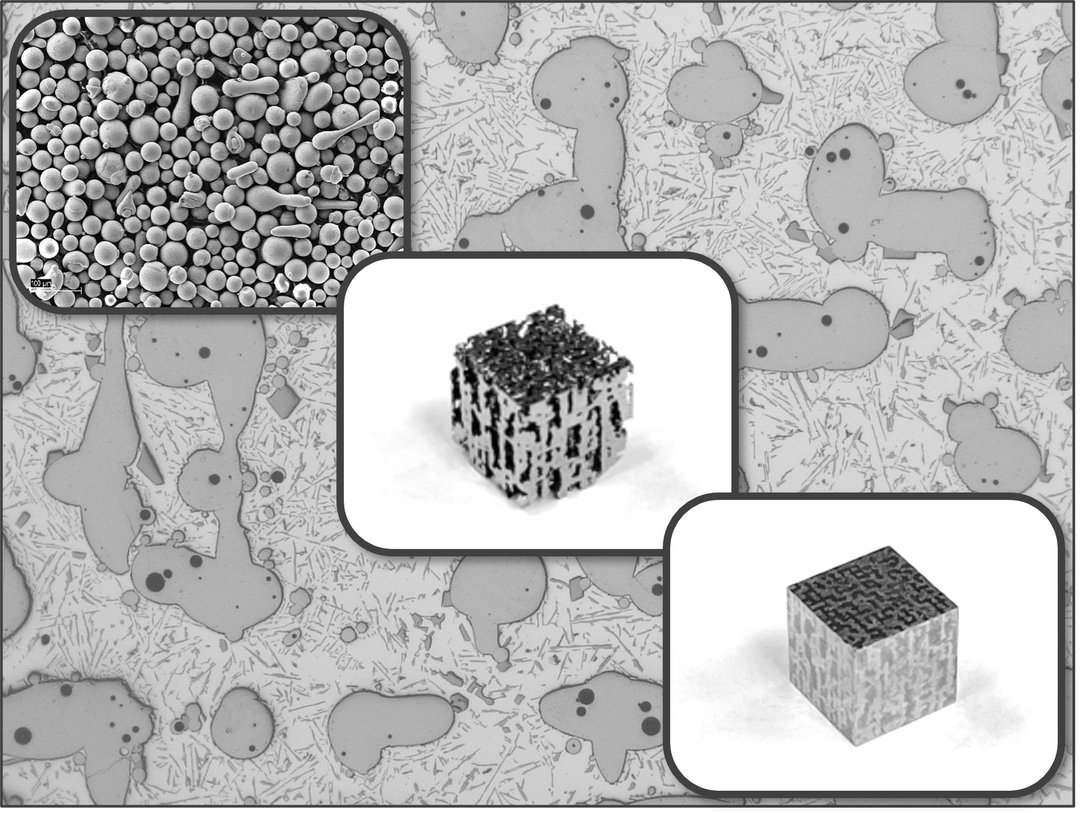
- Phone: +49 821 598 - 69177
Email: kerstin.dittmann@mrm.uni-augsburgmrm.uni-augsburg.de ()
Additive manufacturing of temperature sensitive actuators
Content:
As part of the project, a manufacturing process for temperature-sensitive composite actuators consisting of a polymer matrix and wires made of a shape memory alloy was developed based on the Arburg plastic freeformer. Pre-stressed wires can be deposited during the printing process to produce actuators with high geometric complexity. The interface properties as well as the quasi-static and cyclic mechanical properties of the composite were characterised and modelled to map process-structure-property relationships. The focus was on the thermomechanical properties in order to determine the activation temperatures as a function of the preload as well as the forces that can be applied and on the optimisation of the polymer-wire interface. Following systematic material selection, adaptation of the surface pre-treatment of the wire and development of the printing process, a functional demonstrator in the form of a two-finger gripper was designed and manufactured.
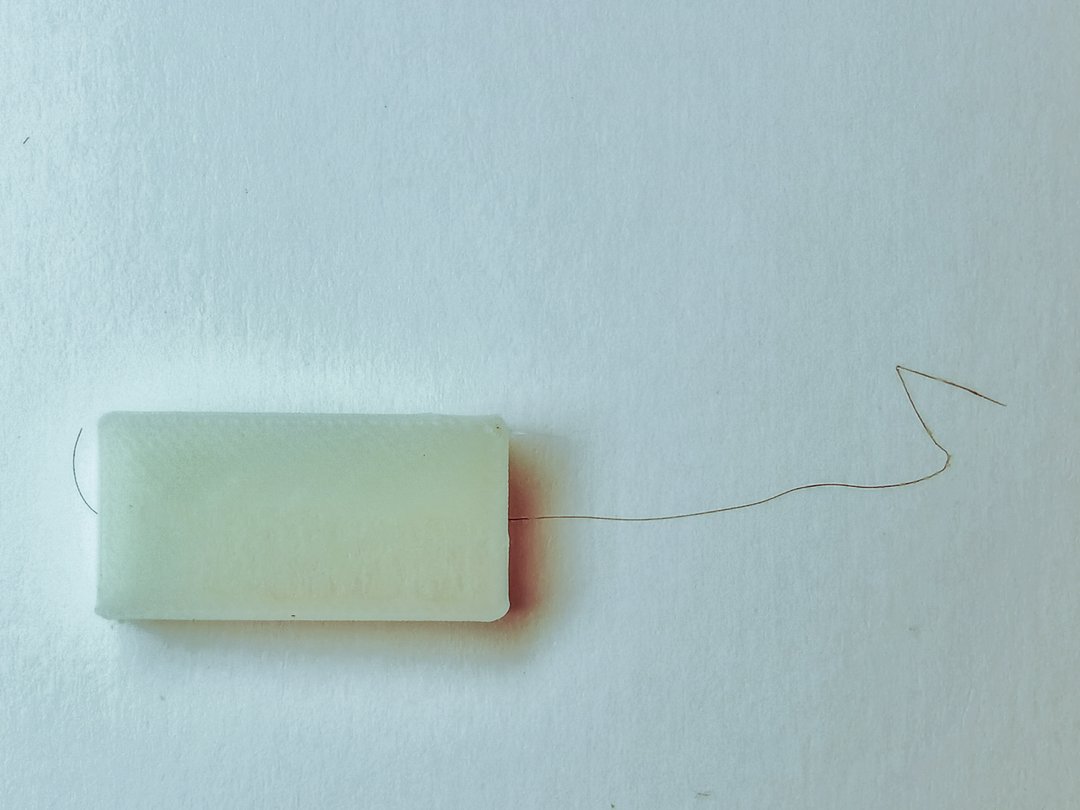
- Phone: + 49 821 598 - 69160
Email: kay.weidenmann@mrm.uni-augsburgmrm.uni-augsburg.de ()
WiR - Wissentransfer Region Augsburg - Digital Engineering and Automation
Funded by: BMBF – Innovative Hochschule – Exzellenzstrategie des Bundes
Duration: 2018-2023
Mechanical Engineering (Prof. M. Sause)
Content:
The project WiR dealt with the possibilities of designing knowledge transfer and the establishment of an innovation laboratory in the field of "Digital Engineering and Automation“. Robot-supported component testing was established in close cooperation with the Institute for Software and Systems Engineering. The aim was to enable mechanical testing of components using free force and moment vectors. For this purpose, a worldwide unique test bench was realized, comprising two 6-axis large payload industrial robots applying the loads to the component under test. Furthermore, relevant testing scenarios were outlined and secondary testing methods (e.g. Acoustic Emission Analysis, Digital Image Correlation) were developed further towards the requirements of component testing as well as different technical installations (e.g. CNC milling machine, 6-axis industrial robot, additive manufacturing) were equipped with a total of 24 different monitoring systems.
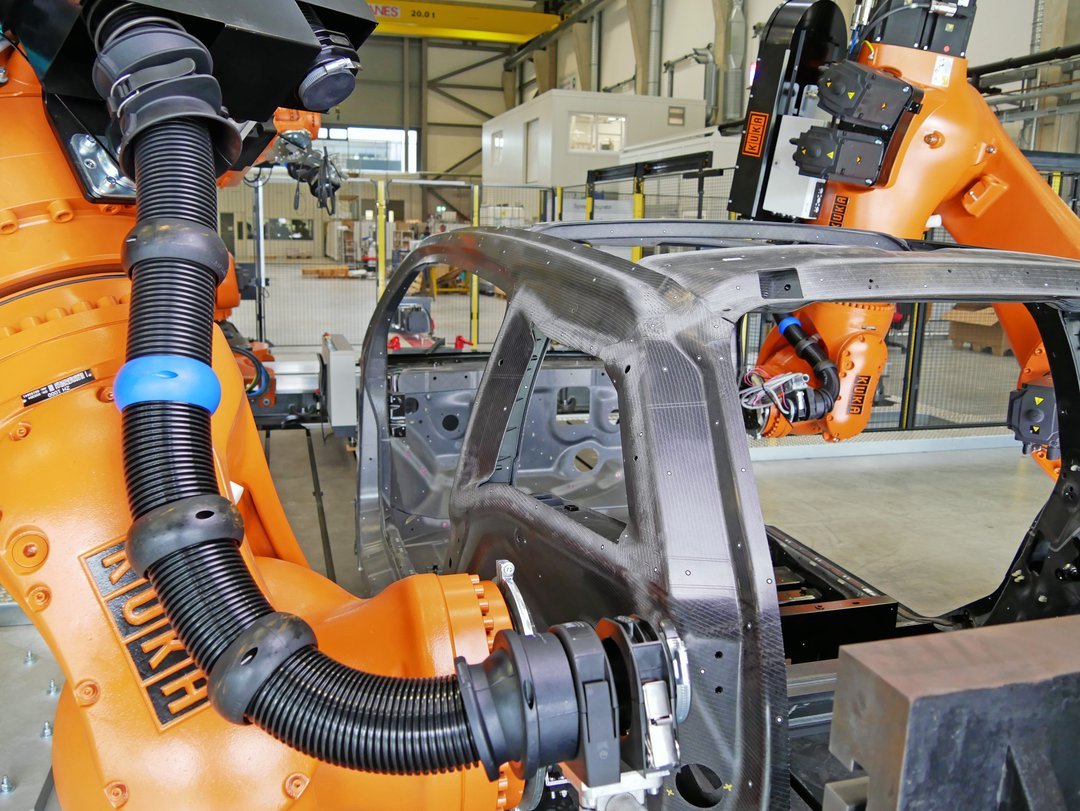
- Phone: +49 821 598 - 69161
Email: markus.sause@mrm.uni-augsburgmrm.uni-augsburg.de ()
MAI CC4 HybCar – Technologien zur effizienten Herstellung von hybriden CFK/Metall-Strukturbauteilen im Automobilbereich
Funded by: Campus Carbon 4.0 – Neue Werkstoffe Bayern
Duration: 2017-2021
Mechanical Engineering (Prof. M. Sause)
Content:
For the use of fiber composites and CFRP-metal hybrids in the series production of automobiles, the automation of the production process is of very high importance. Within the scope of this project, work was therefore carried out on a new type of load-path-oriented material system and a suitable automated manufacturing process. It was focused on the characterization of the interface between metal and CFRP, as well as the forming behavior of the hybrid component.
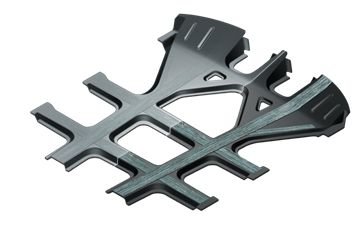
- Phone: +49 821 598 - 69161
Email: markus.sause@mrm.uni-augsburgmrm.uni-augsburg.de ()
MAI CC4 COSIMO – Composites for sustainable Mobility
Funded by: Campus Carbon 4.0 – Neue Werkstoffe Bayern
Duration: 2018-2021
Mechanical Engineering (Prof. M. Sause)
Content:
The goal of the project was the conceptual design and optimization of a T-RTM process to develop the basis for sustainable and efficient manufacturing processes in automotive and aircraft construction. For process monitoring and economic validation of the component quality, a sensor network of ultrasonic, pressure, temperature and dielectric sensors has been developed to be integrated in the T-RTM tool.
In designing the process monitoring, the focus was on evaluating the flow front dynamics and the degree of polymerization. Thus, the sensor network of ultrasonic sensors could be used to interpolate the propagation of the flow front and visualize it over the process time.
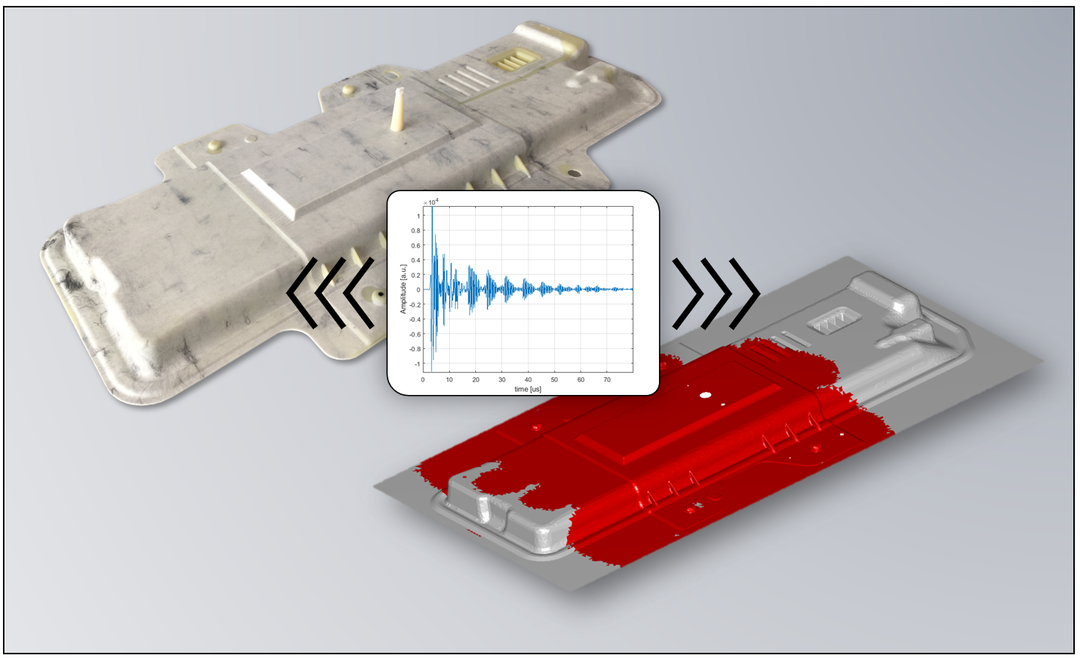
- Phone: +49 821 598 - 69161
Email: markus.sause@mrm.uni-augsburgmrm.uni-augsburg.de ()
MAI CC4 FASTMOVE – Carbon-Hochgeschwindigkeits-5-Achssystem für die Bearbeitungsaufgaben der Zukunft
Funded by: Campus Carbon 4.0 – Neue Werkstoffe Bayern
Duration: 2017-2021
Mechanical Engineering (Prof. M. Sause)
Content:
As part of the project, a structural health monitoring system was developed for a 5-axis CNC milling machine. With this, the condition of the structural components of the milling machine could be monitored live by means of several acoustic measurement methods. In addition, the sharpness of the drill bit's cutting edges could be determined via structure-borne sound measurements and, at the same time, the machined component could be checked for defects.
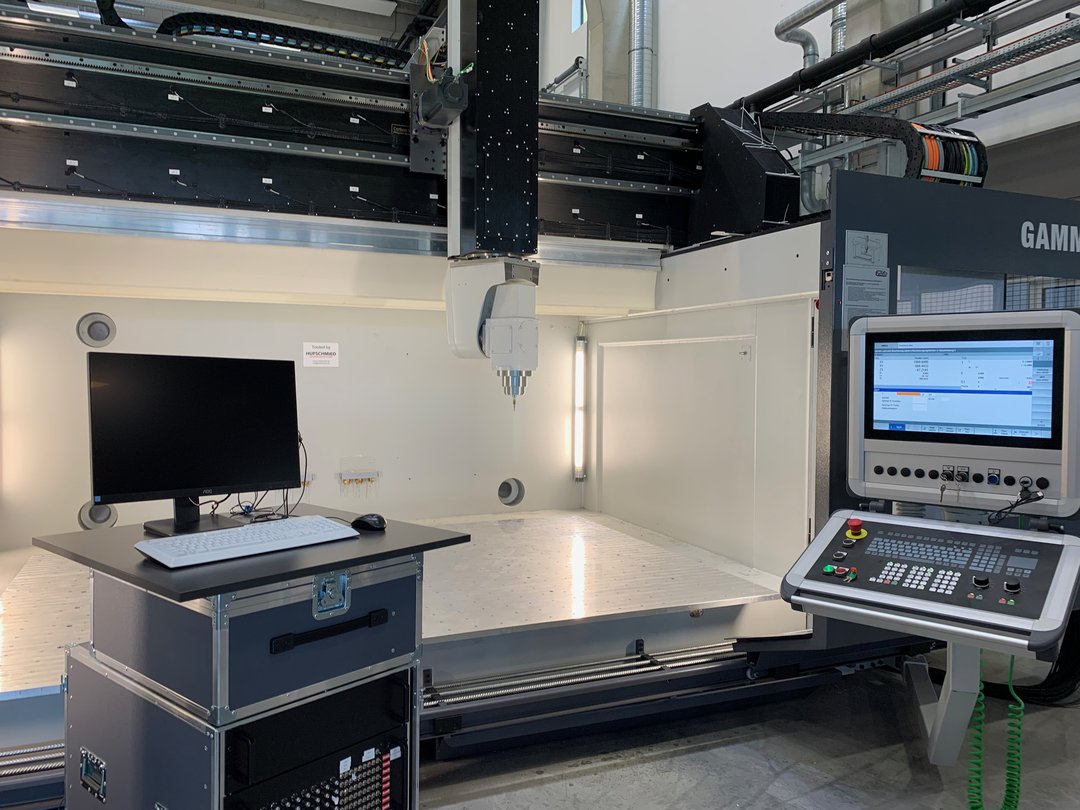
- Phone: +49 821 598 - 69161
Email: markus.sause@mrm.uni-augsburgmrm.uni-augsburg.de ()
MAI CC4 Hybrid – Hybrid composite laminates and joining technologies
Funded by: Campus Carbon 4.0 – Neue Werkstoffe Bayern
Duration: 2017-2021
Mechanical Engineering (Prof. M. Sause)
Content:
As part of the project, test methods for characterizing fiber-metal laminates were developed and brought together for in-situ tests. These resulting parameters made it possible to model the forming processes of the thermoplastic-based hybrid laminate semi-finished products.
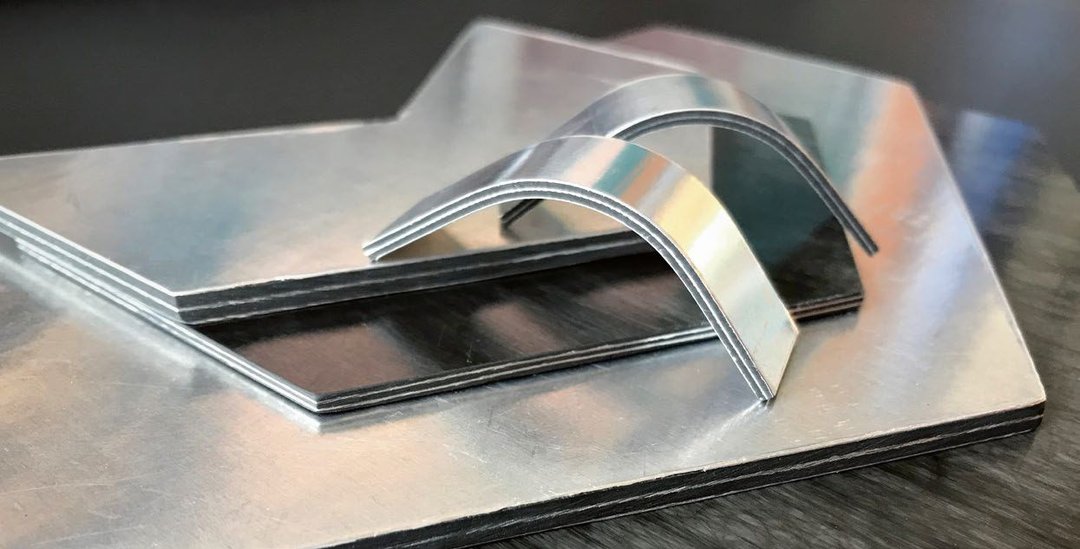
- Phone: +49 821 598 - 69161
Email: markus.sause@mrm.uni-augsburgmrm.uni-augsburg.de ()
MakeKryo – Material characterization at cryogenic temperatures
Funded by: DLR Space Administration
Duration: 2020-2021
Mechanical Engineering (Prof. M. Sause)
Content:
The aim of the project was to develop new testing solutions for the mechanical characterization of fiber composites under space conditions. Test devices were tested which can be used to determine compression and shear characteristics at temperatures down to 20 K. Valid results were obtained for various fiber composites.
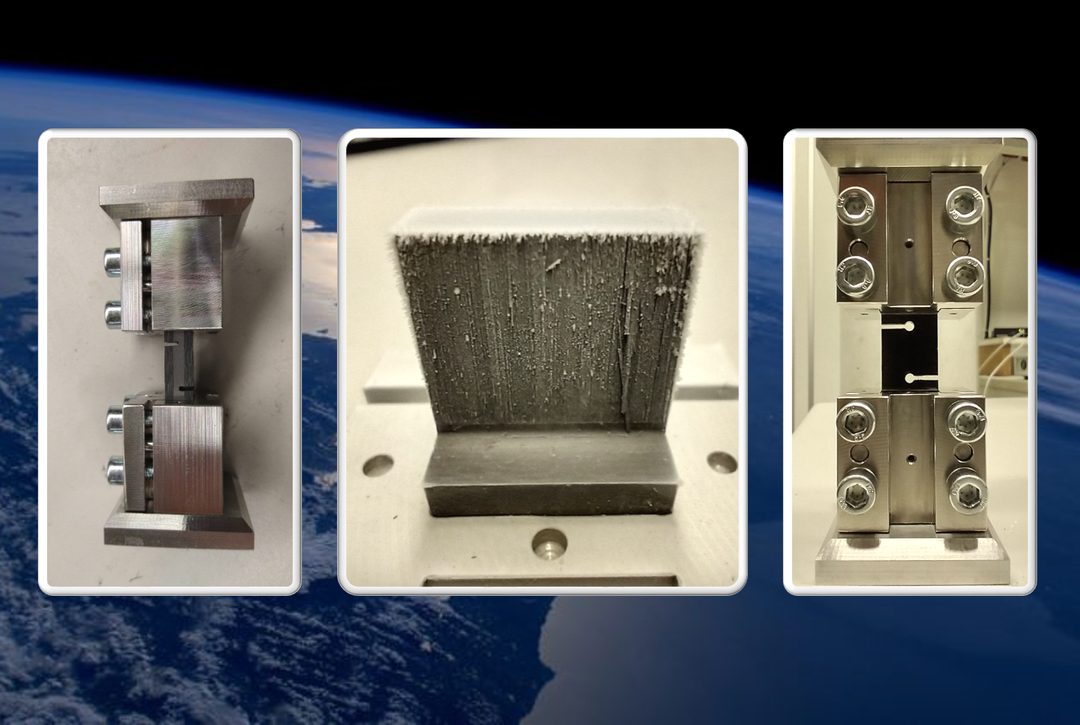
- Phone: +49 821 598 - 69161
Email: markus.sause@mrm.uni-augsburgmrm.uni-augsburg.de ()
Relation of electromagnetic and acoustic emission to temporal and spatial crack motion on a microscopic scale in polymers and carbon fibers
Funded by: DFG Sachbeihilfe
Duration: 2018-2021
Mechanical Engineering (Prof. M. Sause)
Content:
Within the framework of this project, the fundamental relationships of the formation of electromagnetic emission (EME) in polymers, reinforcing fibers and composites were investigated. At the same time, a measurement technique was established to record such EME in typical laboratory experiments and a theoretical model was developed to describe the EME source.
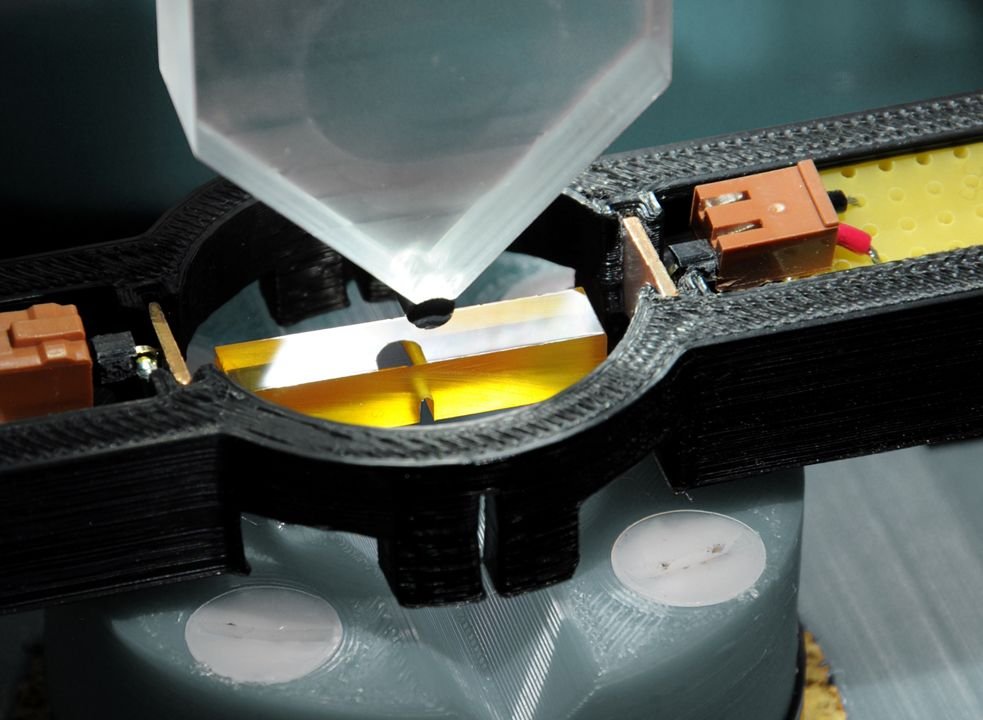
- Phone: +49 821 598 - 69161
Email: markus.sause@mrm.uni-augsburgmrm.uni-augsburg.de ()
MAI ZfP - Combined non-destructive testing methods for quality assurance of fiber reinforced composites
Content:
Within the MAIzfp project, round robin tests of NDT methods were organised, automated test solutions further developed and the modelling of NDT methods more closely examined. Particular attention was paid to the investigation of porosity, fibre waviness and impact damage in fibre composites.
(BMBF, Leading-Edge Cluster MAI Carbon)
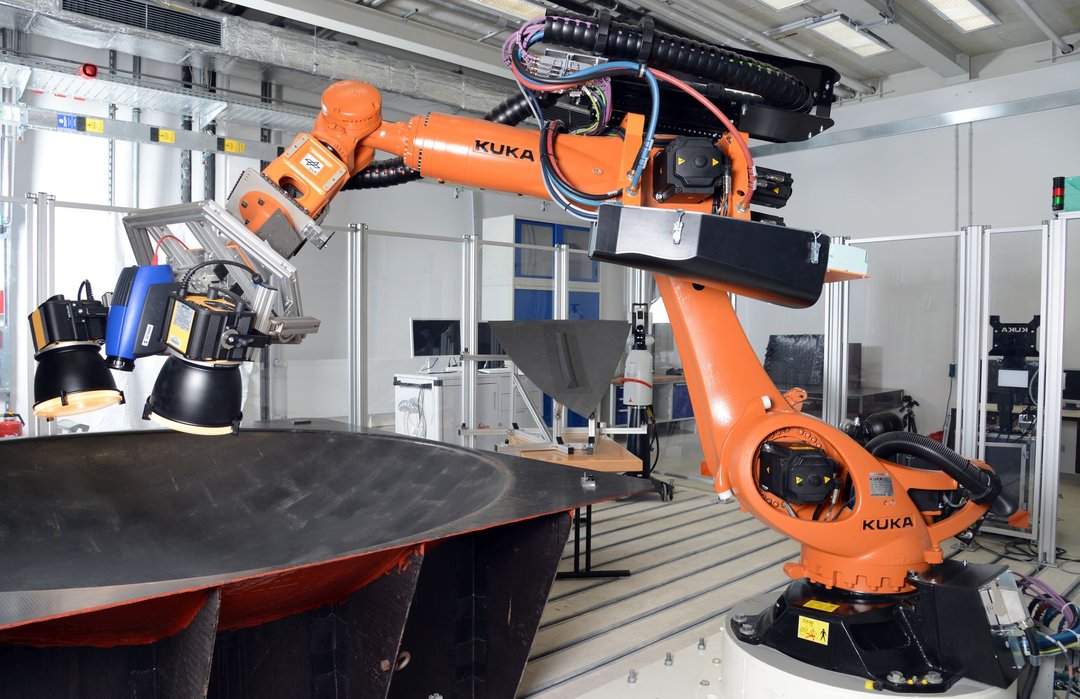
- Phone: +49 821 598 - 69161
Email: markus.sause@mrm.uni-augsburgmrm.uni-augsburg.de ()
MAI Plast - Development of cost-effective processing technologies for automated processing of high-performance thermoplastic composites for high-volume applications
Content:
Within the scope of the project the consolidation and deconsolidation as well as the forming behaviour of fibre-reinforced thermoplastics were investigated. For automated tape laying processes their implications were determined, and for PA-6 the influence of crystallinity on material properties was determined.
(BMBF, Leading-Edge Cluster MAI Carbon)
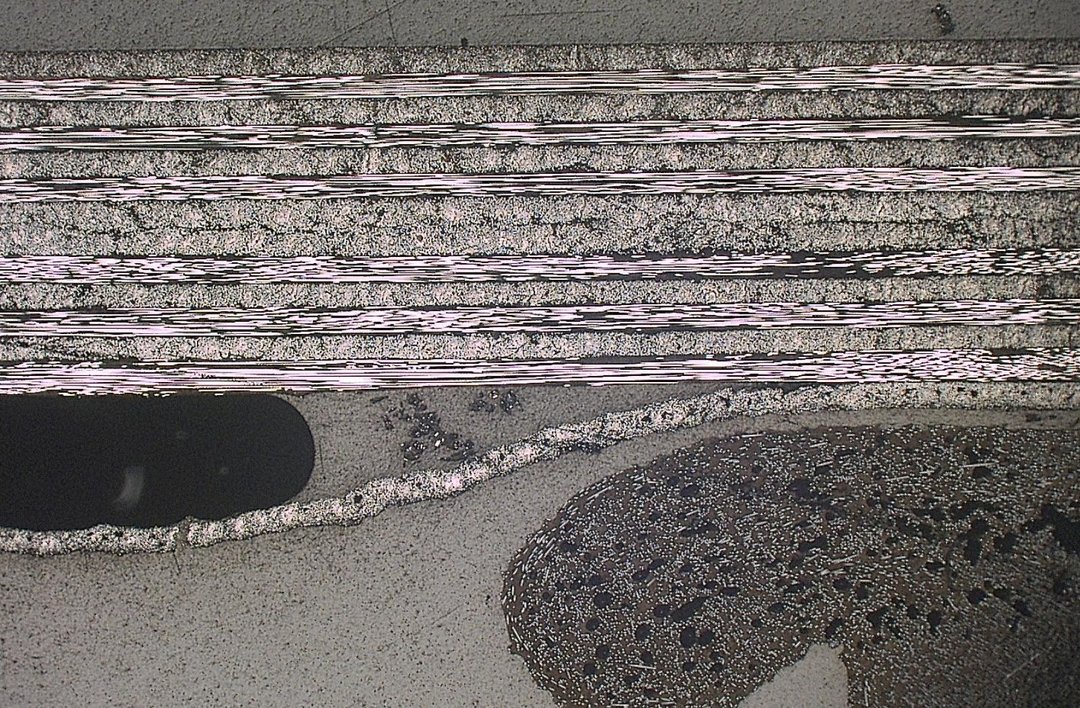
- Phone: +49 821 598 - 69161
Email: markus.sause@mrm.uni-augsburgmrm.uni-augsburg.de ()
FORCIM³A - CFRP/metal composite research association for mechanical and plant engineering
Content:
Interfacial modifications of metal-CFK hybrid layered composites were investigated. The use of modern coating methods significantly increased adhesion and prevented contact corrosion.
(Bavarian Research Foundation)
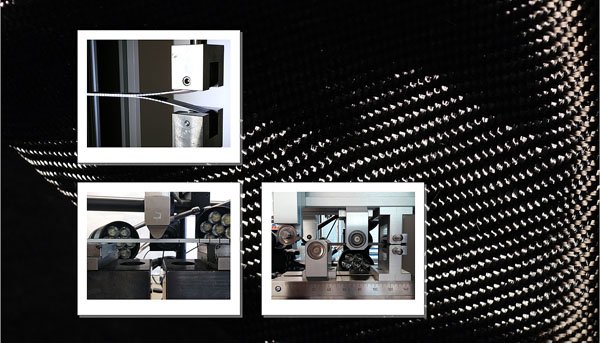
- Phone: +49 821 598 - 69161
Email: markus.sause@mrm.uni-augsburgmrm.uni-augsburg.de ()
ComBo - Efficient manufacturing technology for composite booster segments
Content:
Within the framework of the project, manufacturing technologies for future boosters of the ARIANE-6 program were investigated. The main focus was on the production with automated tape laying processes for thermoplastic CFRP tapes, as well as the monitoring of material development with test methods such as acoustic emission analysis.
(Bavarian Ministry of Economic Affairs, Regional Development and Energy)

- Phone: +49 821 598 - 69161
Email: markus.sause@mrm.uni-augsburgmrm.uni-augsburg.de ()