RG Materials and Mechanics
Group leader
- Phone: + 49 821 598 - 69162
- Email: anna.trauth@mrm.uni-augsburgmrm.uni-augsburg.de ()
- Room 2011 (Building W)
Research
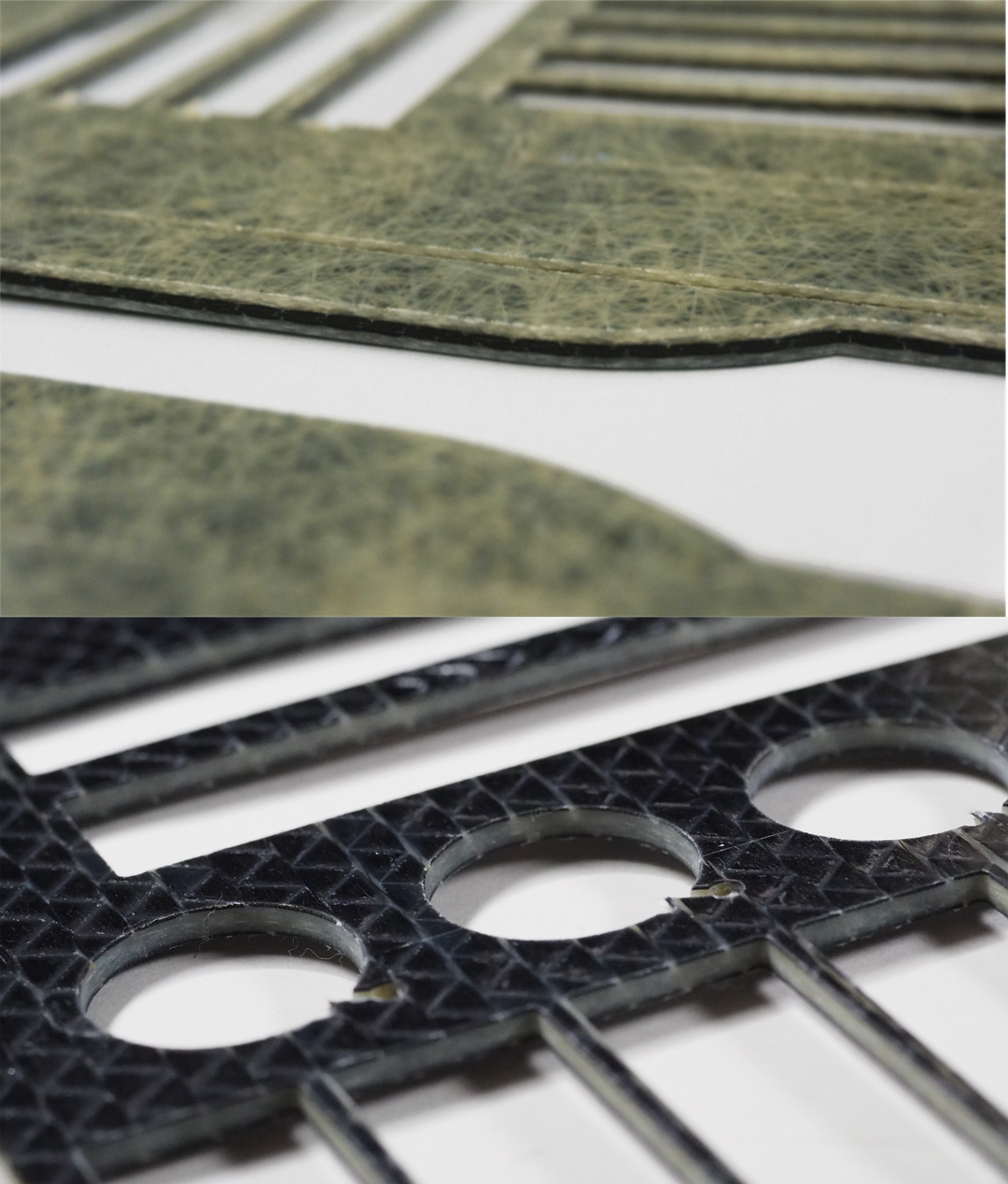
A resource-saving, sustainable use of materials requires new structural materials that can be adapted to a specific requirement. Hybrid material systems are particularly suitable for this purpose. By combining several materials, they allow an optimized range of properties which can be adapted to the given requirements. The development and use of novel hybrid material combinations is always closely related to resource efficiency. It is crucial that not only new, energy-efficient manufacturing processes are developed, but also that the reliable prediction of material and structural properties enables the targeted use of materials. Furthermore, the topic of recycling is becoming more and more important, so that thermoplastic-based fiber composite structures, activatable interfaces and self-reinforced plastics and biopolymers in particular offer a promising approach. Understanding the properties of modern structural materials is indispensable for the targeted use of hybrid material systems. In particular, composites and hybrid material composites lead to the development of new materials by combining different materials and the associated, sometimes macroscopic, inhomogeneity and anisotropic properties pose particular challenges in experimental characterization and in the modeling of material and structural
properties. The research group "Materials and Mechanics" is therefore mainly concerned with the development of methods for the characterization of hybrid material systems and the new and further development of multi-scale modeling approaches.
Method development for the experimental characterization of hybrid material systems
The research activities of the research group "Materials and Mechanics" focus on the one hand on the materials characterization of composite materials and material composites for lightweight construction by means of destructive and non-destructive methods. Of particular importance is the investigation of process-property relationships and the relationship between microstructure and (macroscopic) mechanical properties. In addition to fiber-reinforced polymers, composites with metallic matrix and intrinsically manufactured hybrid material systems, especially fiber-metal laminates, are considered. The portfolio of applied methods includes different scales (sample scale as well as structural and component level) and is based on the representation of different load profiles (quasi-static, dynamic and cyclical). Materials testing is accompanied by optical, locally resolvable determination of characteristic
values by means of digital image correlation.
Since there are usually no standardized procedures available for the characterization of hybrid material composites, research activities are particularly aimed at the adaptation of existing characterization methods and method development. Procedures and methods are being developed to investigate interfacial properties and to investigate lifetime considerations, among other things. In this context, particularly complex loads based on a combination of mechanical, thermal and chemical loads are considered.
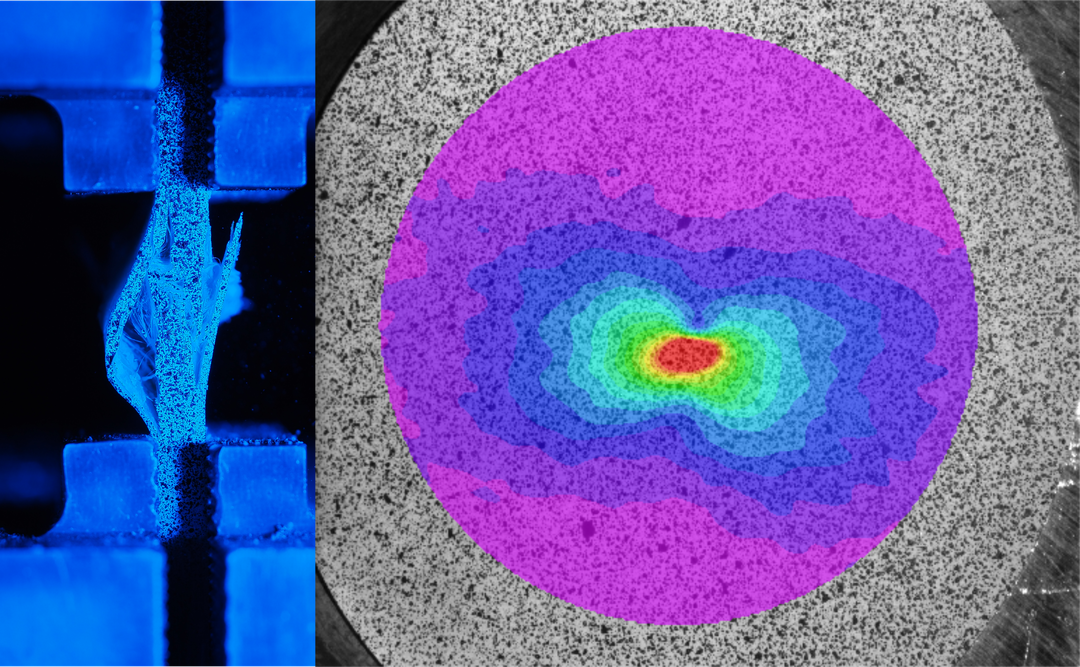
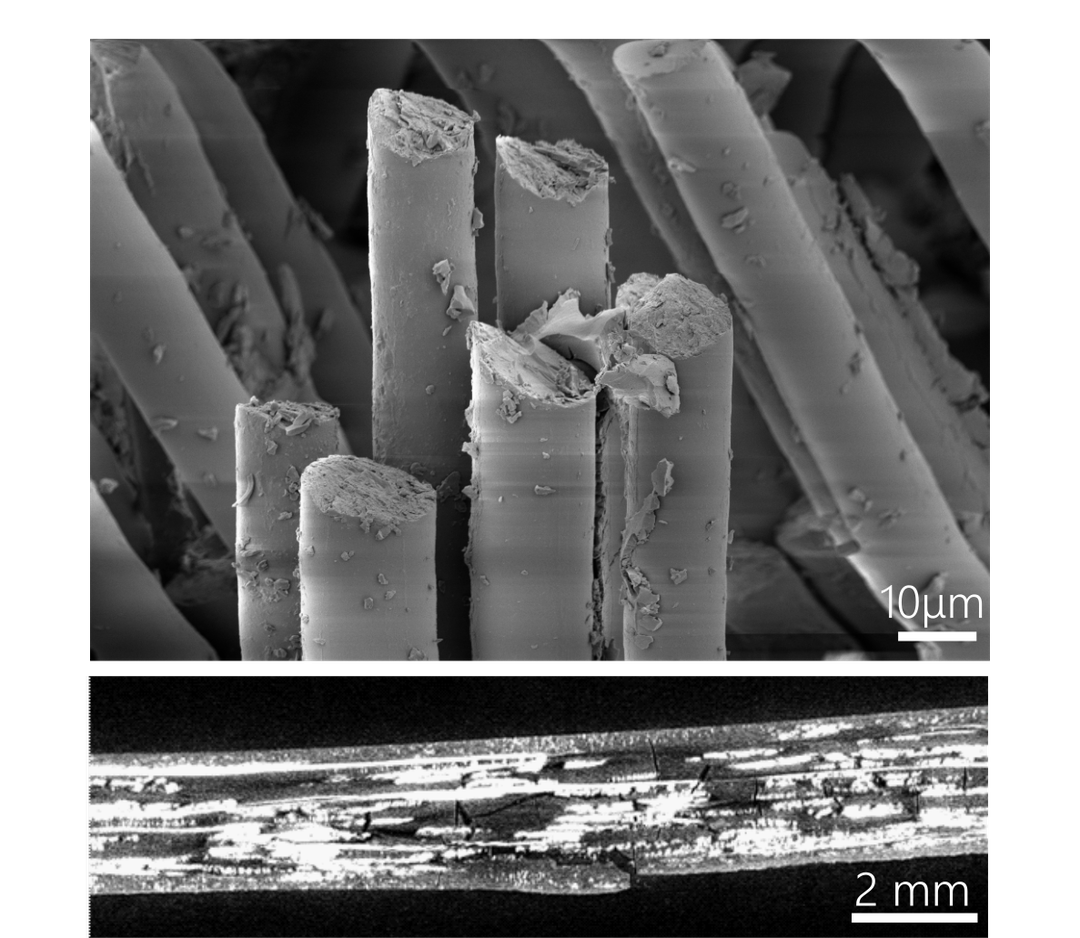
Description of the damage behavior of hybrid material systems
A further research focus is the investigation of the failure behavior and damage evolution of composites and hybrid material composites. The integration of in-situ testing methods, such as acoustic emission, scanning electron microscopy or computed tomography, is crucial to investigate mechanical stress and damage evolution simultaneously. The post-mortal examination of damaged structures completes the analysis of occurring failure mechanisms.
Novel approaches in the field of material modeling
The research activities are rounded off by the adaptation and development of multi-scale modeling approaches for mapping the mechanical material and structural properties of composite materials and hybrid material composites. In addition, destructive and non-destructive testing methods are numerically represented in order to validate and further develop characterization methods and strategies.
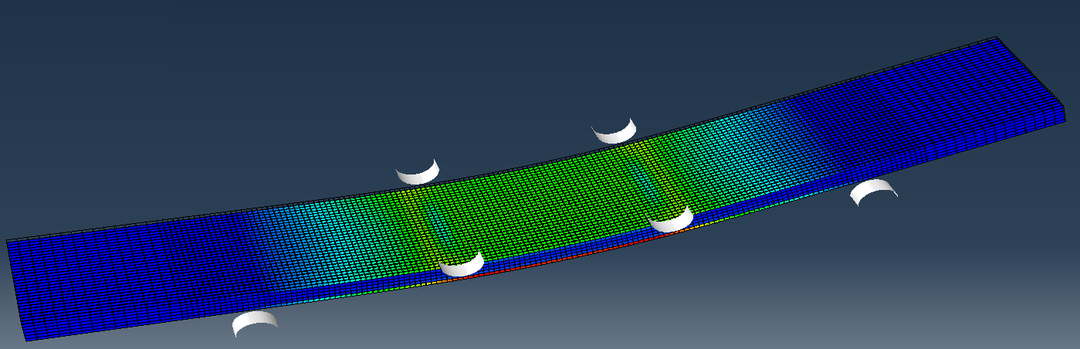
Team
Scientific Assistants
- Phone:
- Email: leonard.gabele@mrm.uni-augsburgmrm.uni-augsburg.de ()
- Room 2019 (Building W)
- Phone:
- Email: holger.haefele@mrm.uni-augsburgmrm.uni-augsburg.de ()
- Room 2019 (Building W)
- Phone: +49 821 598 - 69175
- Email: kiran.kamath@uni-auni-a.de ()
- Room 2019 (Building W)
- Phone: +49 821 598 - 69161
- Email: sophia.keller@fh-welsfh-wels.at ()
- Phone: +49 821 598 - 69171
- Email: marco.korkisch@mrm.uni-augsburgmrm.uni-augsburg.de ()
- Room 2018 (Building W)
- Phone: +49 821 598 - 69161
- Email: maximilian.linde1@porscheporsche.de ()
- Phone:
- Email: julia.reichmann@mrm.uni-augsburgmrm.uni-augsburg.de ()
- Room 207 (Building WALTER Technology Campus Augsburg / Halle 43 Future Fabrication)
- Phone:
- Email: nora.schorer@mrm.uni-augsburgmrm.uni-augsburg.de ()
- Phone: +49 821 598 - 69161
- Email: anton.weiss@th-degth-deg.de ()
- Phone: +49 821 598 - 69163
- Email: sarah.enzler@uni-auni-a.de ()
- Room 2016 (Building W)
- Phone: +49 821 598 – 69167
- Email: quirin.schneider@uni-auni-a.de ()
- Room 2019 (Building W)
Current research projects
Information on our current research projects can be found here.