Mit KI-Assistenz den Glasverlust reduzieren
KI-gestützte Optimierung der Kühlanlagen-Technologie im Glasanlagenbau kann umfassend Ressourcen sparen
Die Universität Augsburg und die Firma Grenzebach arbeiten gemeinsam an einer KI-gestützten Optimierung der Kühlanlagen-Technologie im Glasanlagenbau. Dadurch sollen umfassend Ressourcen geschont werden. 20 Jahre - so lange sind die Anlagen zur Glasproduktion der schwäbischen Firma Grenzebach ohne Unterbrechung im Einsatz. Grund ist die Produktionslinie, deren Anfang ein Hochofen zur Glasschmelze bildet und der nie abgeschaltet wird. Fortwährend entsteht Glas und durchläuft einen manuell gesteuerten Abkühlprozess, der viel Erfahrung benötigt. Die Anlage für diesen Produktionsschritt, den sogenannten Kühlkanal, optimieren Forschende des KI-Produktionsnetzwerks am Lehrstuhl für Produktionsinformatik an der Universität Augsburg in Zusammenarbeit mit der Forschungs- und Entwicklungsabteilung von Grenzebach. „Wenn durch einen Fehler bei der Einstellung des Kühlkanals Glas von schlechter Qualität entsteht, verarbeiten die Hersteller es zu Scherben und schmelzen diese erneut ein. Allerdings ist das nur zu einem gewissen Grad möglich und die bei der Herstellung eingesetzte Energie ist verloren“, erklärt Tom Röger, der bei Grenzebach die Abteilung „Data Sciences“ aufbaut und das Projekt betreut. In Zahlen ausgedrückt: Pro Stunde Produktionsausfall würden geschätzt bis zu 50 Tonnen Glas vernichtet und 107.000 KWh für die Rückführung in den Prozess benötigt werden. Das entspräche dem Jahresverbrauch von 46,5 deutschen Haushalten. „Das möchten wir ändern, unsere Anlagen mittels KI optimieren beziehungsweise die Bedienung erleichtern. Hierfür benötigten wir zusätzliche Expertise, der Lehrstuhl für Produktionsinformatik der Universität Augsburg hat sich als vertrauensvoller Partner angeboten“, erläutert Röger die Projekthintergründe. Zurzeit erstellen die Forschungspartner einen digitalen Zwilling des Kühlkanals. „Ein digitaler Zwilling ist ein digitales Abbild eines physischen Bauteils, eines Prozesses oder einer Anlage. Durch die Nutzung von Echtzeitdaten aus dem Produktionssystem bildet er eins zu eins die Wirklichkeit ab und an ihm simulieren wir den Abkühlprozess sowie den Kühlkanal,“ erklärt Prof. Dr.-Ing. Johannes Schilp, Leiter des Lehrstuhls für Produktionsinformatik und universitätsseitig verantwortlich für das Projekt. „Künstliche Intelligenz sorgt für die nötige Geschwindigkeit: Die Simulation soll in Echtzeit laufen, wohingegen die Rechenleistung ohne KI Tage in Anspruch nehmen würde“, ergänzt Ludwig Vogt, Projektmitarbeiter. Der Digitale Zwilling löst ein spezifisches Problem des Glasanlagenbaus: „Der unseren Anlagen im Betrieb vorgeschaltete Hochofen läuft ohne Unterbrechung, da ein Abschalten das Glas noch im Ofen erstarren lassen würde und das Aufheizen bis zur Glasschmelze viel Energie benötigt. Unsere Industriepartner können zu Testzwecken also nicht einfach die Produktion stoppen“, erläutert Röger. Der digitale Zwilling ist folglich der erste Schritt auf dem Weg zu optimierten Anlagen. Ziel des Projekts ist es, aufbauend auf dem digitalen Zwilling ein vollautomatisiertes System zur Steuerung des Kühlkanals zu entwickeln. „Wenn der Kühlvorgang, beispielsweise bei einer neuen Produktionscharge mit anderen Glasdicken, angepasst werden muss, soll der digitale Zwilling die idealen Temperaturzonen berechnen. Diese werden den Anlagenbedienenden vorgeschlagen. KI und menschliche Erfahrung sorgen somit schlussendlich für einen optimalen Herstellungsprozess“, skizziert Johannes Schilp. Neben der Energie- und Ressourcenersparnis soll auch Zeit gewonnen werden: Je nach Erfahrung der Mitarbeitenden dauern Änderungen der Produktion derzeit zwischen einer halben und vier Stunden. Dies soll um bis zu 50% verringert werden. In den folgenden beiden Projektjahren soll nun der Prototyp aufgebaut und die Validierung des KI-gestützten Modells an realen Anlagen erfolgen. „In unserer gemeinsamen Forschungskooperation können wir damit aufzeigen, wie durch Digitalisierung und KI erhebliche Effizienzsteigerungen im Betrieb von Produktionsanlagen erreicht werden können“, erklärt Johannes Schilp abschließend. Das KI-Produktionsnetzwerk Augsburg ist ein Verbund der Universität Augsburg, des Fraunhofer-Instituts für Gießerei-, Composite- und Verarbeitungstechnik IGCV, des Zentrums für Leichtbauproduktionstechnologie (ZLP) des Deutschen Zentrums für Luft- und Raumfahrt (DLR) in Augsburg sowie der Hochschule Augsburg. Beteiligt sind zudem regionale Industriepartner. Ziel ist eine gemeinsame Erforschung KI-basierter Produktionstechnologien an der Schnittstelle zwischen Werkstoffen, Fertigungstechnologien, datenbasierter Modellierung und digitalen Geschäftsmodellen. Der Freistaat Bayern fördert das Projekt mit 92 Millionen Euro im Rahmen der Hightech Agenda Plus.
E-Mail:
johannes.schilp@informatik.uni-augsburginformatik.uni-augsburg.de ()
E-Mail:
manuela.rutsatz@presse.uni-augsburgpresse.uni-augsburg.de ()
Ressourcen schonen und Bedienung erleichtern
Ein digitaler Zwilling als Problemlöser
Das Ziel: Eine vollautomatisierte Anlage
Das KI-Produktionsnetzwerk Augsburg
Wissenschaftlicher Kontakt
Medienkontakt
Pressebilder zum Download
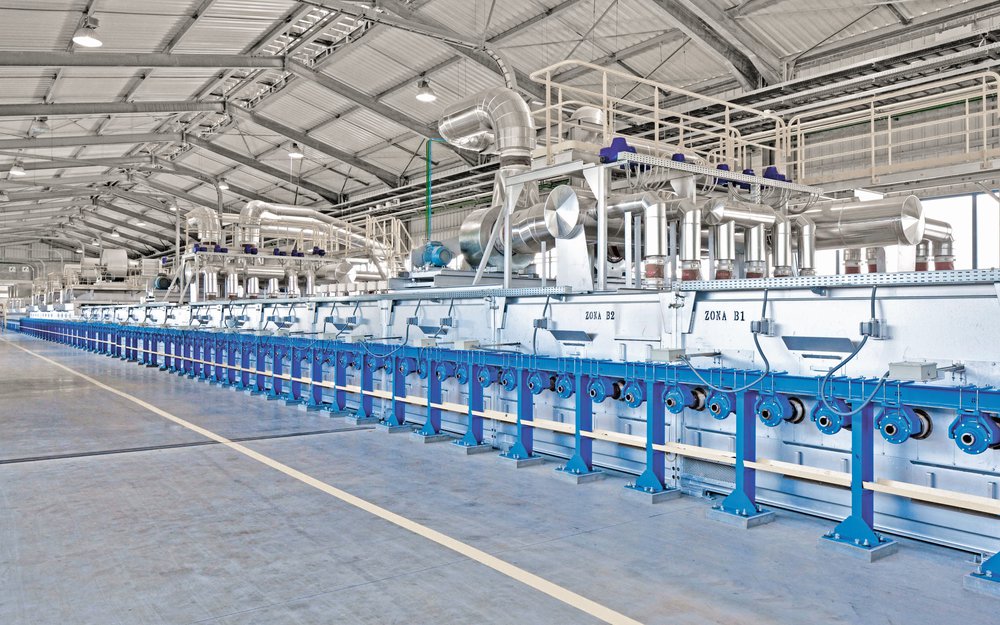